Discovering the Secrets: How Lifepo4 Batteries Are Made?
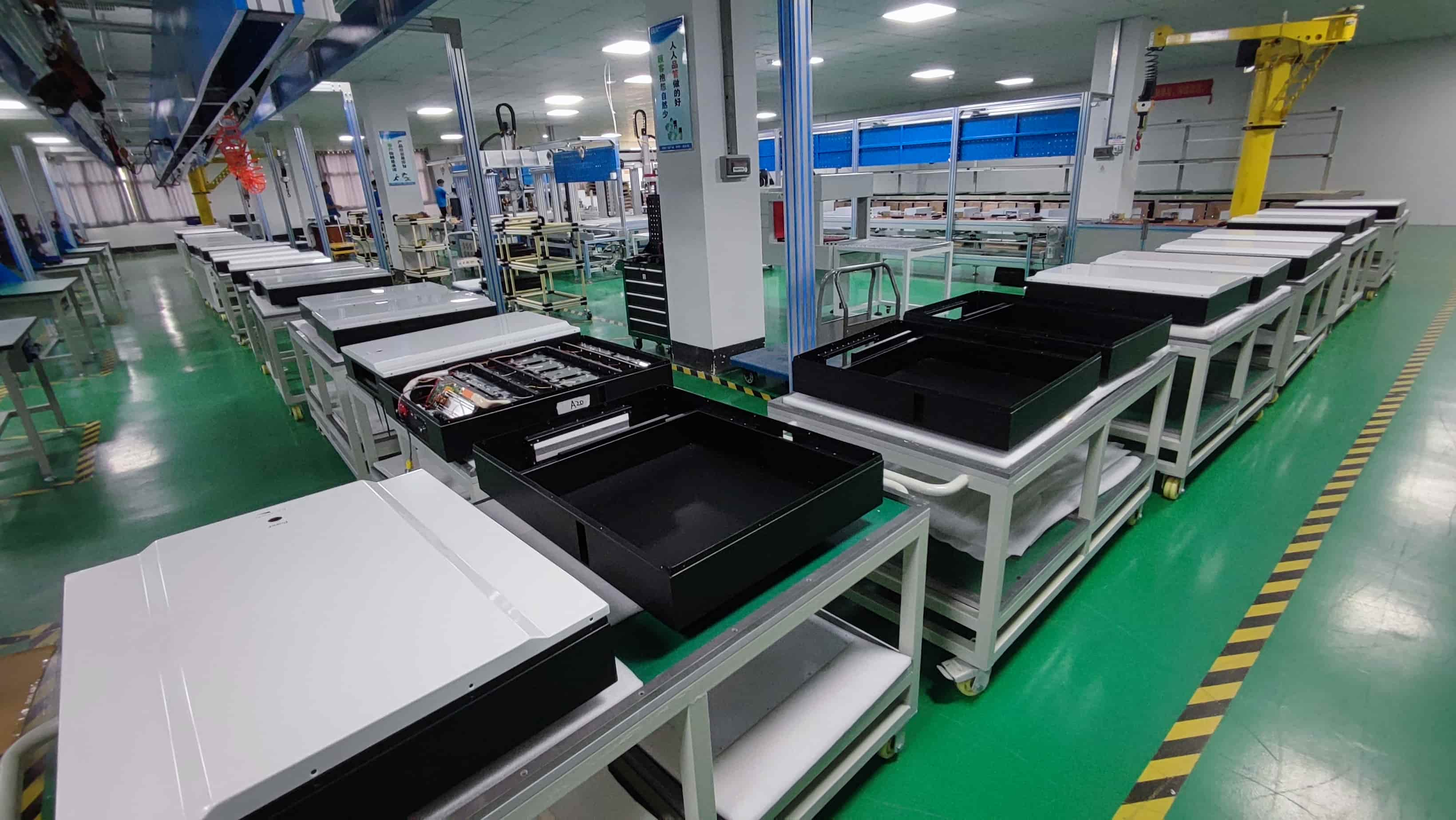
Lithium iron phosphate (LiFePO4) batteries are a type of rechargeable battery that has become increasingly popular due to their high energy density and low self-discharge rate. They have been used for many applications, ranging from consumer electronics to electric vehicles. In this article, we will take an in-depth look at how LiFePO4 batteries are made, including the materials and processes involved in their production.
The manufacturing process of LiFePO4 batteries involves several steps which include mixing raw materials, forming electrodes, assembling cells and encapsulating them into final products. The most important part of manufacturing is making sure that the components are of good quality before assembly. To ensure that the components meet safety requirements, they must be tested multiple times throughout the process.
To make LiFePO4 batteries with high performance and reliability, careful attention must be paid during each stage of the manufacturing process. In particular, special care should be taken when selecting materials and controlling temperature levels for various parts as these factors play a significant role in determining the ultimate performance of the product. By understanding all aspects of LiFePO4 battery production, manufacturers can produce reliable products with optimal performance characteristics.
Definition
Lithium-ion phosphate (LiFePO4) batteries are a type of rechargeable battery that has gained popularity in recent years due to their high energy density, long cycle life and low cost.
LiFePO4 cells have been used for applications ranging from electric vehicles to consumer electronics such as laptops and cell phones. The production of LiFePO4 cells involves several steps, starting with the selection of raw materials and ending with the assembly of finished battery packs.
The first step in making a LiFePO4 battery is selecting the appropriate raw materials. These include lithium metal oxide, graphite anode material, electrolyte solution, separator membrane and current collectors. Each component must be chosen carefully in order to ensure that the final product meets safety standards and performs optimally.
Once the components have been selected, they must then be processed according to their respective requirements before being assembled into cells or packs. This usually includes mixing powders together, coating electrodes with active materials, forming electrodes into specific shapes, filling them with electrolyte solution and sealing them together under vacuum conditions.
After this process is completed, each individual cell is tested to ensure it meets all specifications before being incorporated into larger packs or modules for use in applications requiring more power output.
#1 Lifepo4 Cells Production
Production 1: Raw Material Preparation
Positive electrodes are made from lithium iron phosphate (LiFePO4), negative electrodes are made from graphite or other carbonaceous material, separators between them are made from polymers like polyethylene or polypropylene, and electrolytes consisting of salts dissolved in organic solvents like ethylene carbonate or dimethyl carbonate. All these parts are carefully inspected for defects prior to assembly into cells - one mistake could lead to catastrophic failure down the line!
Production 2: Positive Electrode Manufacturing
The positive electrodes are made up of three parts: The active material, the conductive agent, and the binder. In order to create these components:
- Firstly an active material such as a lithium iron phosphate (LFP) powder or graphite must be created. This is done by crushing minerals into small particles and then blending them with various chemicals that make them suitable for use in batteries;
- A conducting substance like carbon black needs to be added to help facilitate electron flow between the cells;
- Finally, a binding agent must be used so that all the materials stick together when formed into shapes for use in batteries.
The resulting mixture can then be applied onto thin sheets of aluminum foil which have been pre-coated with adhesive as part of their manufacturing process. These laminates are then stored until required for battery assembly.
Positive electrodes require careful handling due to their highly flammable nature - they should always be handled in accordance with safety regulations and best practices regarding fire prevention and protection methods established within the workplace environment.
Production 3: Negative Electrode Manufacturing
According to surveys, around 90% of all lifepo4 battery cells are powered by negative electrodes made from graphite. This material provides an excellent conductive medium while also being lightweight and cost-effective.
- Graphite particles are cut into nanometer size and combined with a binder material such as polyvinylidene fluoride (PVDF), evenly distributed throughout the battery structure.
- These powder particles are pressed together using a specialized machine called a "calendar". During this pressing process, heat and pressure combine to form a solid graphite sheet shaped to design specifications.
- When complete, this sheet will become the negative electrode assembly inside each individual lifepo4 battery.
To ensure optimum performance over the long term, quality control measures must be taken at every stage of manufacturing. These include careful monitoring of particle size distribution, moisture levels and other parameters required for production precision.
Production 4: Cathode And Anode Assembly
First, the electrodes must be prepared for assembly. The mixing process involves combining carbon black powder with either graphite or artificial graphite powders with conductive agents such as acetylene black and then adding binder solutions such as polyvinylidene fluoride (PVDF) solution to create a uniform mixture. This mixture will become the electrode material for both the positive and negative sides of the battery cell.
Once this is done, it's time to assemble the cathode and anode into their respective structures:
Cathode Assembly:
- A separator sheet is placed between two layers of electrode material which are laminated together using pressure rollers at high temperatures.
- Connectors are attached to each side of the laminate so they can connect to other parts within the battery pack.
- Finally, nickel-plated copper tabs are connected to complete the cathode assembly.
Anode Assembly:
- The anode also consists of two layers but instead of laminating them together, they're simply stacked on top of one another and pressed into place by hand.
- Nickel-coated steel connectors are added onto each side of the stack before nickel tabs are soldered onto those same connectors to complete the anode assembly.
Depending on the battery design, the electrodes are interleaved and wound into cylindrical or prismatic shapes. Windings are carefully controlled to ensure proper alignment and even distribution of material. Then they'll finally come together inside a completed battery cell housing unit ready for use.
Production 5: Electrolyte Filling
The next production stage is filling it with electrolytes. A combination of ethylene carbonate, dimethyl carbonate, and lithium hexafluorophosphate is added to the cell through an injection port. The mixture enables electrical current to flow between the electrodes when voltage is applied across them. After the mixture has been injected into the cell, it must be sealed to ensure that no material can escape or enter during operation.
Production 6: Lifepo4 Cell Sealing
The last step in the lifepo4 cell production process is sealing. In this procedure, a sealant material is used to create an airtight enclosure for the cells and prevent potential contamination or leakage of electrolytes. Sealing can be done using various techniques such as compression welding, hot-melt adhesive application, ultrasonic bonding, laser welding and heat staking.
Method | Advantages | Disadvantage |
---|---|---|
Compression Welding | Durable seal Fast processing time Low-cost materials required | High temperature needed Limited design flexibility |
Hot-Melt Adhesive Application | Flexible design Heat resistance Very low energy input | Poor mechanical strength Long curing times |
Ultrasonic Bonding | Fast production rate Can bond multiple layers simultaneously Good structural integrity & electrical insulation properties | Higher-cost equipment needed Not suitable for large parts |
Laser Welding | No contact with part surfaces Precise control over weld size and shape Less stress on components than other methods | Expensive equipment required Complex programming of machine settings necessary |
Heat Staking | Easy integration into automated assembly lines Minimal deformation of the part surface during the bonding process Little requirement for handling after forming operation has been completed | Time-consuming setup procedures |
Production 6: Cells Seal Test
Tests conducted after sealing include verifying if there were any leaks and visual inspection for signs of damage. Leakage tests involve pressurizing the case containing the battery and examining whether gas escapes from any point on its surface under pressure. Visual inspections are used to check if there are any deformities on either side of the casing caused by poor sealing processes or other external forces such as manufacturing defects or mishandling.
#2 Lifepo4 Battery Pack Assembly
The lifepo4 battery pack assembly is a complex process that symbolizes the intricate workings of life itself. It begins with individual cells, each one meticulously crafted and tested for quality assurance. These cells are then connected in series or parallel to assemble larger modules that have specific voltage requirements based on the application they will be used for.
Next, an enclosure must be designed to protect the module from outside elements such as water, dust or extreme temperatures. This enclosure can range from simple plastic shells to metal cases depending on the desired level of protection. The interior layout of these enclosures also needs to be planned out carefully so that all electrical connections are secure and minimal heat buildup occurs during operation. Once this is done, components such as circuit boards, wiring harnesses and connectors can be added according to customer specifications. Finally, additional safety features like insulation and fuses may be included before final testing takes place and the battery pack is ready for shipment.
Step 1: External assessment
The first step in the assembly process of a LiFePO4 battery is to inspect each cell for any visible damage. This inspection includes checking if there are any dents, scratches or marks on the casing as well as ensuring all components are present and securely fastened. The inspector must also confirm that the terminals have no corrosion and their contact points are clean. In addition, any signs of discoloration or oxidation in the metal structure should be noted.
During this stage, it is important to check for any irregularities such as short circuits between cells or loose connections which could potentially lead to safety hazards and reduce performance efficiency. Once these issues have been identified, they can be addressed before proceeding with further assembly steps. By inspecting each single cell prior to assembly, manufacturers can ensure that only high-quality batteries will be produced.
Step 2: Measure The Capacity, Internal Resistance, Voltage
The main key to the performance of the lifepo4 battery pack is the consistency of the battery cells. Therefore, before assembly, it is necessary to measure the capacity, internal resistance, and voltage of each single battery. According to the difference of a certain production standard, they are divided into groups and then assembled. The smaller the difference, the better the performance.
The process begins by connecting the battery to a test system that measures its electrical parameters such as open circuit voltage (OCV), short circuit current (SCC) and impedance. OCV is measured at full charge, while SCC readings are taken after the battery has been discharged to 0 volts. Impedance measurements determine how much resistance exists between two terminals when connected by a current or voltage. These parameters provide valuable insight into the overall quality and performance of each LifePo4 battery prior to assembly into packs.
Step 3: Connect in Series into Modules
The voltage of each single lifepo4 cell is 3/3.2V, and the voltage is increased to meet the customer's demand parameters through a series connection.
Therefore, it is first necessary to arrange and fix multiple lifepo4 cells through automatic palletizing, pressing, pneumatic palletizing, laser welding and other methods, to ensure that the lifepo4 battery pack can have a stable structure even under severe shaking, and it is not easy to loosen. In addition, compared with manual welding, laser welding is more efficient, more stable, and has smaller welding errors.
Step 4: Insert Module into Housing
- Check the components of the module for any defects or imperfections.
- If necessary, make adjustments to ensure all parts fit together properly.
- Once everything has been checked and confirmed to be correct, the module can be placed precisely inside the case and screwed into place securely.
Through the above steps, ensure that the entire device is firmly fixed during transportation and use to prevent vibration and shock damage. To further reduce potential problems, additional seals can also be applied where applicable around the edges of the housing to provide additional protection from environmental elements such as dust or moisture ingress.
Step 5: Voltage Sampling Line Installation
This step is to enable an external device or circuit to measure the operating voltage of the battery.
- First, the proper length of the insulated wire must be cut for this procedure.
- Then connect the bare ends to the positive and negative terminals respectively; make sure no short circuits occur during this operation.
- Connect the other end of each wire to an analog-to-digital converter (ADC) port on the microcontroller board or directly to an integrated circuit (IC).
With this connection made, any monitoring system can accurately sample the voltage without fear of negatively affecting its performance. To ensure consistent readings, it is important to ensure that all connections are secure and properly insulated to prevent any potential hazards such as electric shock or current leakage.
Step 6: Arranging The Wiring Harness
At this stage, all components are tested and assembled onto their respective PCBs. A dedicated team of engineers carefully inspects each wire for any signs of damage or irregularities before connecting them to the appropriate terminals.
The harnesses must be aligned so that they do not interfere with each other when the batteries are subsequently stacked on the production line. Any loose strands or incorrect connections need to be corrected immediately or significant delays may result. All cables are then covered with protective insulation and labeled accordingly so technicians can easily identify which wires are connected where during maintenance or troubleshooting operations.
After all the finishing work is done, each unit is checked again for any faults before moving on to the next stage of production.
Step 7: BMS Installation
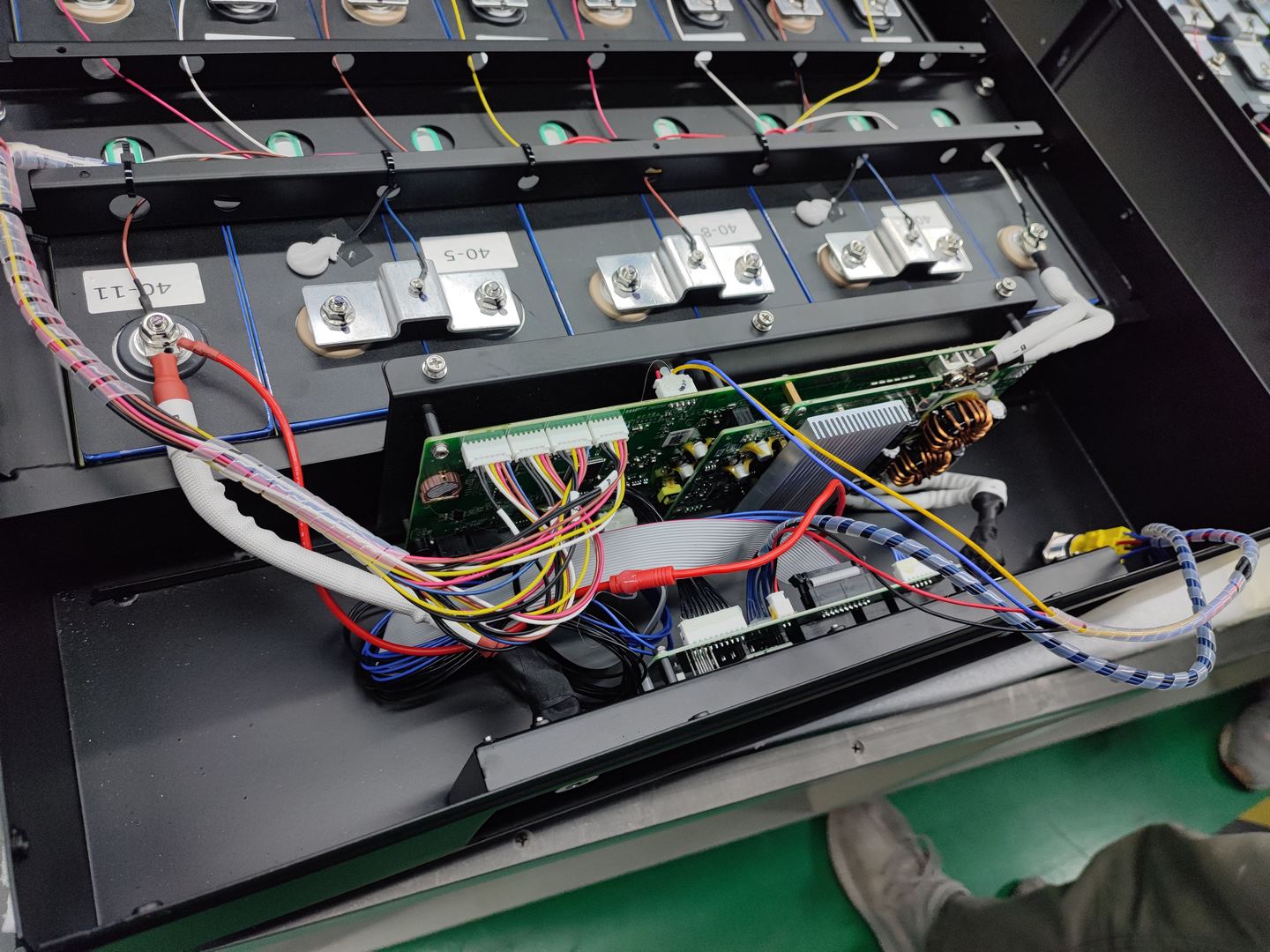
The seventh step in the assembly of a LiFePO4 battery is the installation of a Battery Management System (BMS). A BMS is an electronic circuit that monitors and controls individual cells within a larger battery pack. This ensures optimal performance, safety, and lifetime use of the battery. It also prevents overcharging or discharging of any cell which can lead to decreased efficiency or even catastrophic failure of the entire system.
The BMS is installed by connecting it to each individual cell with wires. The wiring harness must be carefully routed so as not to create interference between different components within the system. Once all connections are properly made, the BMS will power up and begin its monitoring functions automatically. If any abnormalities occur, such as excessive charging or discharging of any single cell, then appropriate action can be taken depending on how the system has been programmed. In this way, the proper functioning of the battery can be maintained for many years without fail.
Step 8: Battery Pack Case Cover Sealing
As the saying goes, "The devil is in the details". The last Assembly Step of building a lithium-ion battery pack involves sealing the case cover to ensure that all components remain protected from outside elements such as dust and water. The following are key points regarding the assembly step:
- A sealant or glue must be applied around the edges of the battery pack's casing before the case cover can be secured.
- Heat shrink tubing may also be used on some models to further protect against moisture damage.
- All exposed terminals should have anti-corrosive grease applied prior to the installation of the case cover.
- Once sealed, wires will need to be routed through designated holes in order to connect with other parts of the battery pack.
- Finally, inspection is necessary after completion of the assembly step to make sure no errors were made during the sealing process.
This last step helps ensure that each individual cell within the battery remains properly insulated and secure so that it can maintain optimal performance throughout its lifetime. By taking all precautions when constructing a lithium-ion battery, users can rest assured their lifepo4 batteries will remain safe and efficient over time.
#3 Testing And Quality Control
Battery cells are complex machines, and every battery must meet strict performance standards. Quality control is an integral part of the lifepo4 manufacturing process. It begins with testing each individual cell before assembly to ensure that it meets a basic set of criteria. Once assembled into a pack, further tests are performed on the entire product.
The purpose of quality control is twofold:
- To detect any faults in components or construction;
- To verify that the finished product complies with customer requirements and industry safety standards.
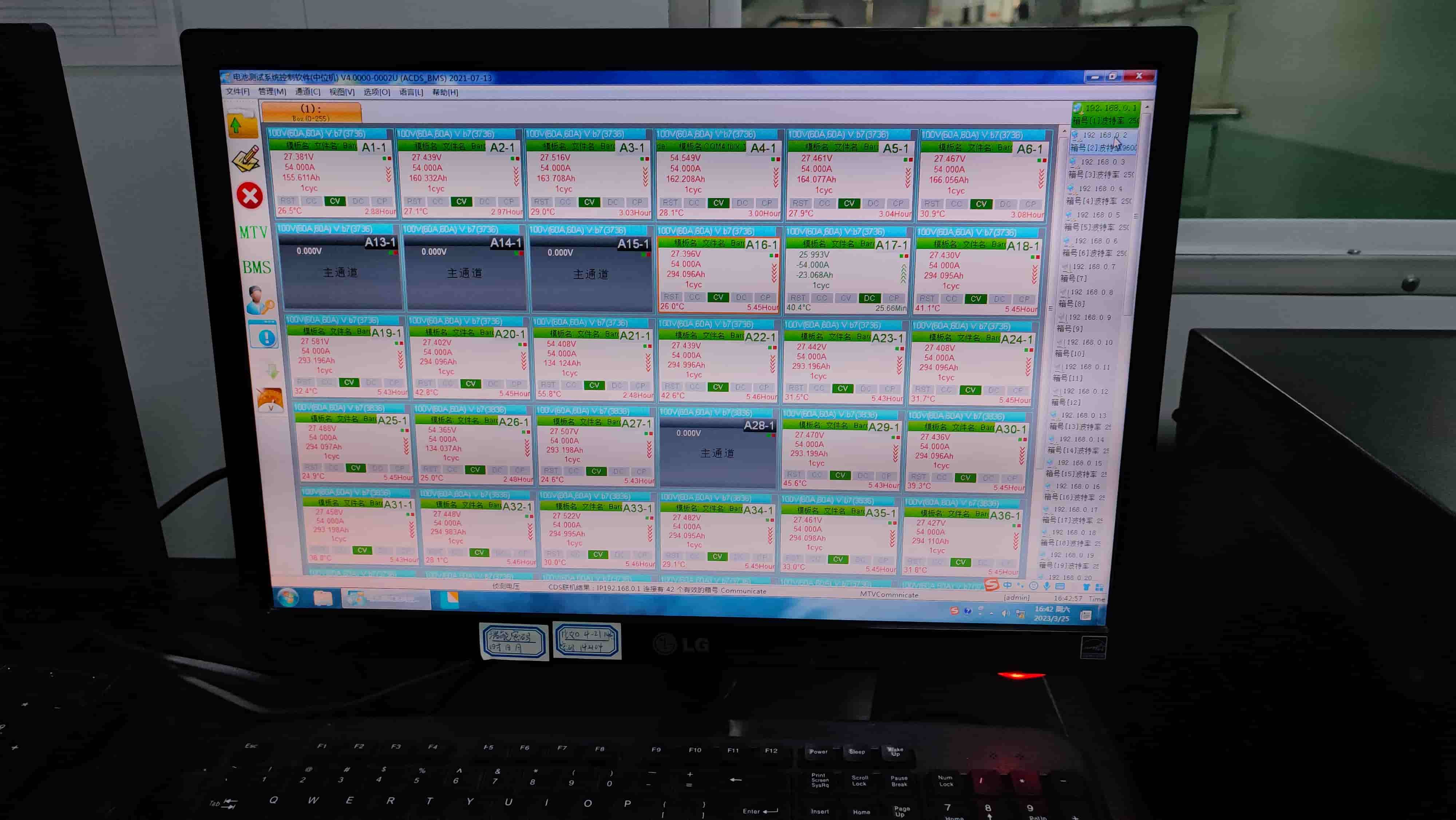
The most important test for lifepo4 batteries is cycle life--the number of charge/discharge cycles the battery can handle without failing prematurely due to capacity loss or other damage.
To perform these tests accurately and objectively, manufacturers use automated equipment such as cyclers and impedance analyzers. These instruments measure various parameters including internal resistance, energy density, temperature rise during fast charging, self-discharge rate over time and many more.
By comparing results from multiple units at different stages of production, manufacturers can quickly identify anomalies and take corrective action if necessary.
If a cell fails any one of these tests, it must be discarded or reworked until it passes all the required criteria. Only after the successful completion of all tests will the battery be released for sale to customers who demand reliable performance from their power sources.
#4 Packaging And Shipping
Once the LiFePO4 cells are manufactured, they must be packaged and shipped to their destination. Packaging is an important step in the manufacturing process as it ensures that nothing can damage or contaminate the cells during transit. Depending on the size of the shipment, different types of packing materials may be used for protection.
For smaller shipments, individual boxes lined with foam or bubble wrap can be used to protect each cell from shock and vibration. For larger orders, multiple layers of corrugated cardboard and stretch film may be employed for extra stability.
It is also critical that all required shipping labels are accurately printed out and affixed to each box before dispatch. These should include basic information such as the sender’s address, receiver’s address, package contents, weight, etc.
In addition, any special instructions requested by customers should also be included on the label either directly or through a bar code scan system if available. This helps ensure smooth delivery without any delays due to mislabeling at customs.
Finally, once all necessary labels have been added to each package, they must then go through quality control checks before being sent off on a pallet or truck depending on the order volume and distance of travel required. Here inspections are conducted to make sure every item has been securely packed according to customer requirements and industry standards before leaving the factory premises.
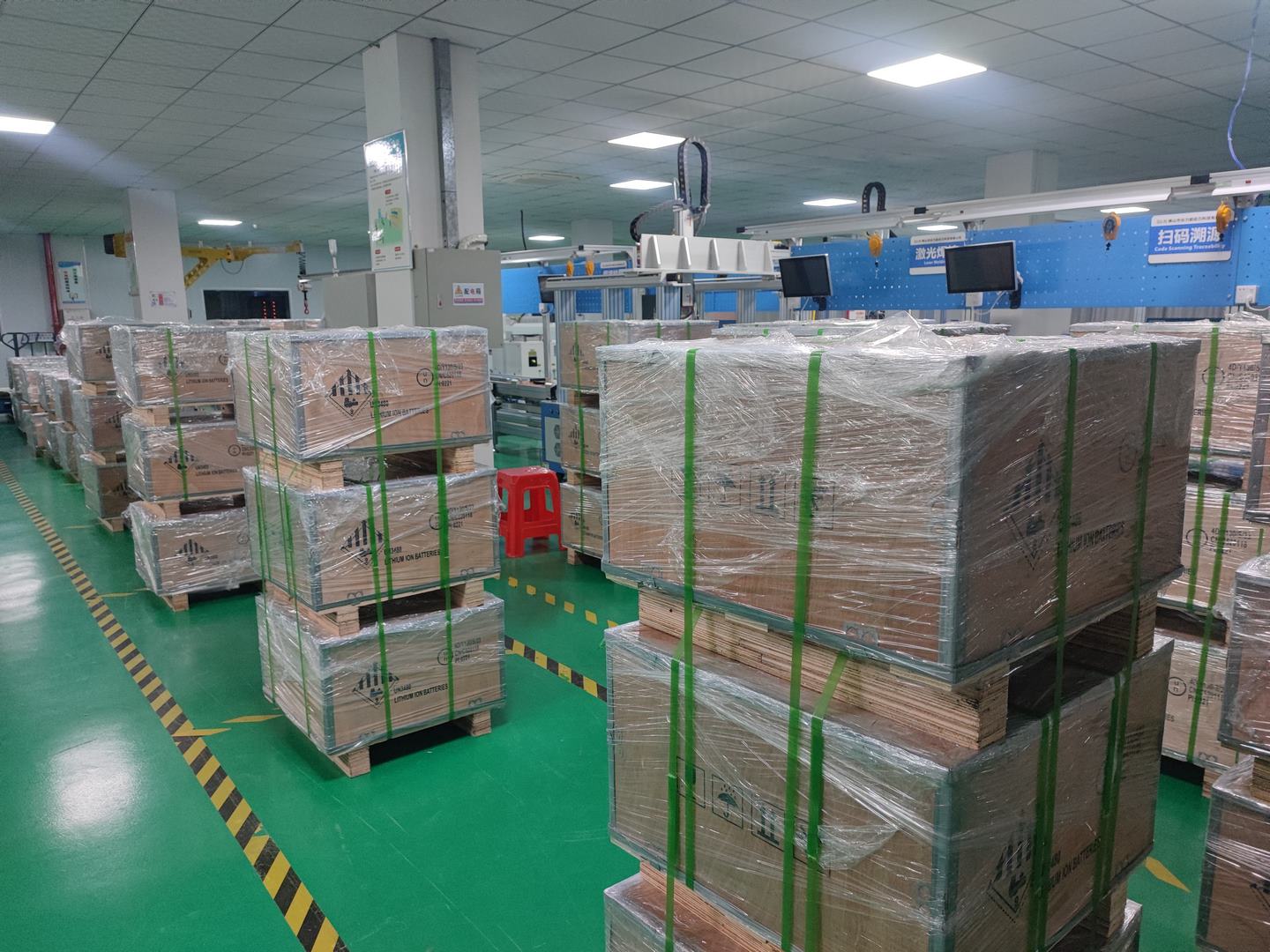
Advantages Of Lifepo4 Batteries
LiFePO4 (lithium iron phosphate) battery is a rechargeable battery that has become more and more popular in recent years. They offer many advantages over other types of lithium-ion and lead-acid batteries and are suitable for a variety of applications in portable electronics, electric vehicles, energy storage devices, and more.
(1) High energy density
According to a 2020 study conducted by Stanford University, lithium iron phosphate batteries have three times the energy density of conventional lead-acid batteries.
(2) Long life
A key advantage of lithium iron phosphate batteries over other types of lithium-ion or nickel-metal hydride batteries is their longer cycle life and therefore longer life. This makes them ideal for use in stationary power systems where they can be expected to undergo frequent discharge/charge cycles over long periods of time without significant degradation in performance.
(3) Wide temperature range
LiFePO4 batteries also tend to run cooler than other battery chemistries, reducing thermal management requirements and improving safety features; this means they can be safely used where extreme temperatures could cause damage or shorten battery life.
(4) High charging and discharging efficiency
Lifepo4 batteries have excellent charge acceptance and are able to quickly reach a full state of charge even after a deep discharge – in some cases, up to 95% within an hour, depending on the application – providing users with better control and convenience.
(5) Low self-discharge rate
Due to its low self-discharge rate, LiFePO4 batteries retain their stored energy better than most other chemistries, allowing extended charge cycles when necessary.
Disadvantages Of Lifepo4 Batteries
LiFePO4 batteries are attractive for a variety of applications because they have high energy density and excellent safety characteristics. However, there are some disadvantages that should also be considered before making an informed decision about the type of battery to use. The following table summarises these drawbacks:
Advantage | Disadvantage |
Long Cycle Life | High Initial Cost |
Low Self-discharge Rate | Temperature Sensitivity |
Good Safety Performance | Reduced Power Density |
High Energy Density | Limited Charging Capacity |
The initial cost of LiFePO4 batteries is higher than other types of rechargeable batteries such as lead acid or NiMH due to their more complex chemistry and manufacturing process.
Additionally, their performance can be adversely affected by extremes in temperature which limits their application range. Furthermore, although offering relatively high energy densities compared to most other chemistries, the power density (the amount of current it delivers) is reduced when compared with nickel-based chemistries.
Finally, while having long cycle lives, LiFePO4 batteries typically offer limited charging capacity; this means they cannot accept large amounts of charge quickly like some other types of battery.
In summary then, despite its many advantages over other technologies, users must consider several factors before selecting LiFePO4 cells for their particular application.
These include the initial cost relative to other chemistries available, how much charge capacity is needed, and whether temperatures outside the recommended operating range will occur during usage. As always, understanding your specific needs is vital in order to make an informed choice about the right technology for you.
Applications Of Lifepo4 Batteries
The applications of LiFePO4 batteries are numerous. They have been used in a wide range of industries, from consumer electronics to energy storage systems.
As previously discussed, LiFePO4 batteries provide higher specific energy and power densities than other lithium-ion chemistries due to their high stability and low reactivity. Additionally, they possess excellent safety characteristics as well as long cycle life and fast charge/discharge times.
In the consumer space, LiFePO4 batteries have found success in powering portable electronics such as laptops, cell phones and electric vehicles (EVs).
Their light weight makes them attractive for use in EVs because it reduces overall vehicle mass for improved performance and fuel efficiency. The same attributes make them ideal for use in solar or wind-powered battery packs that can store the excess renewable electricity generated during peak periods for later consumption.
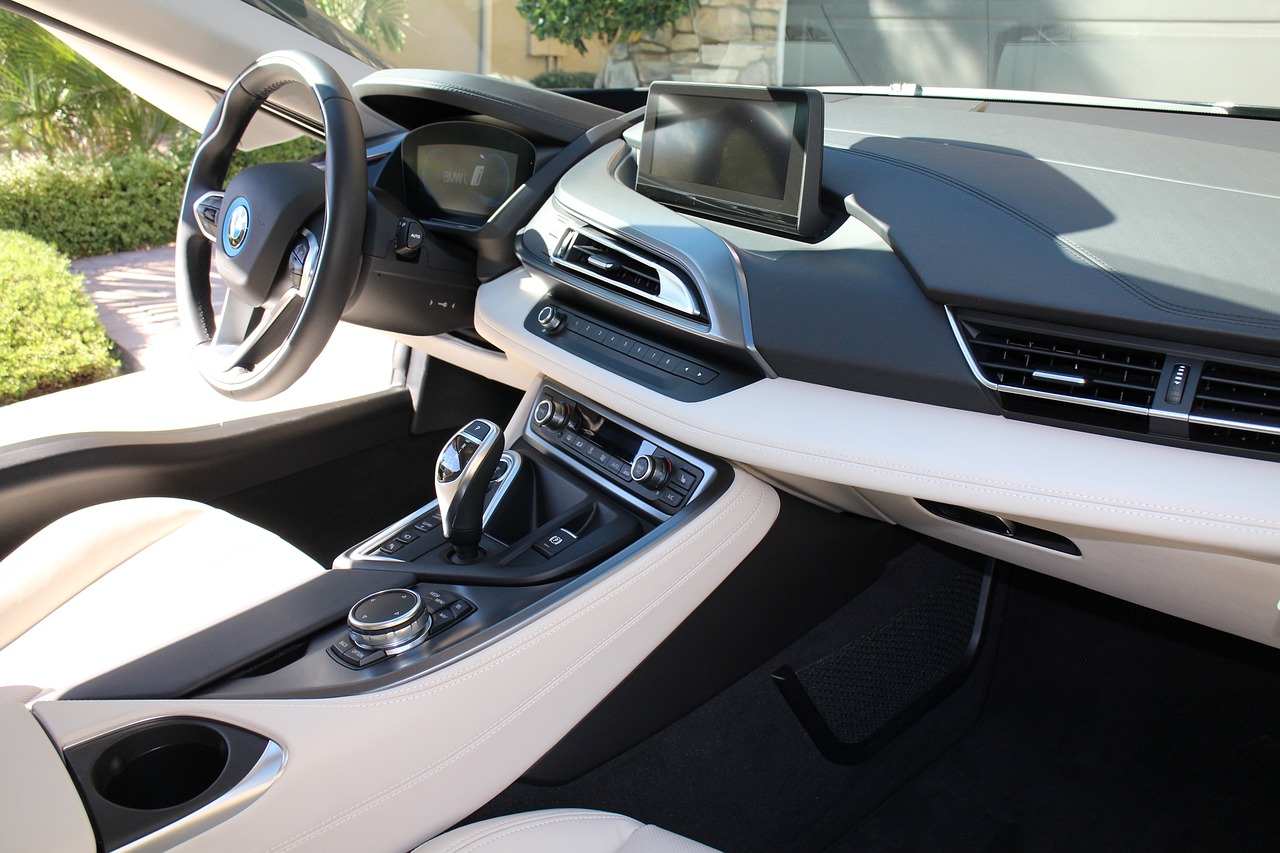
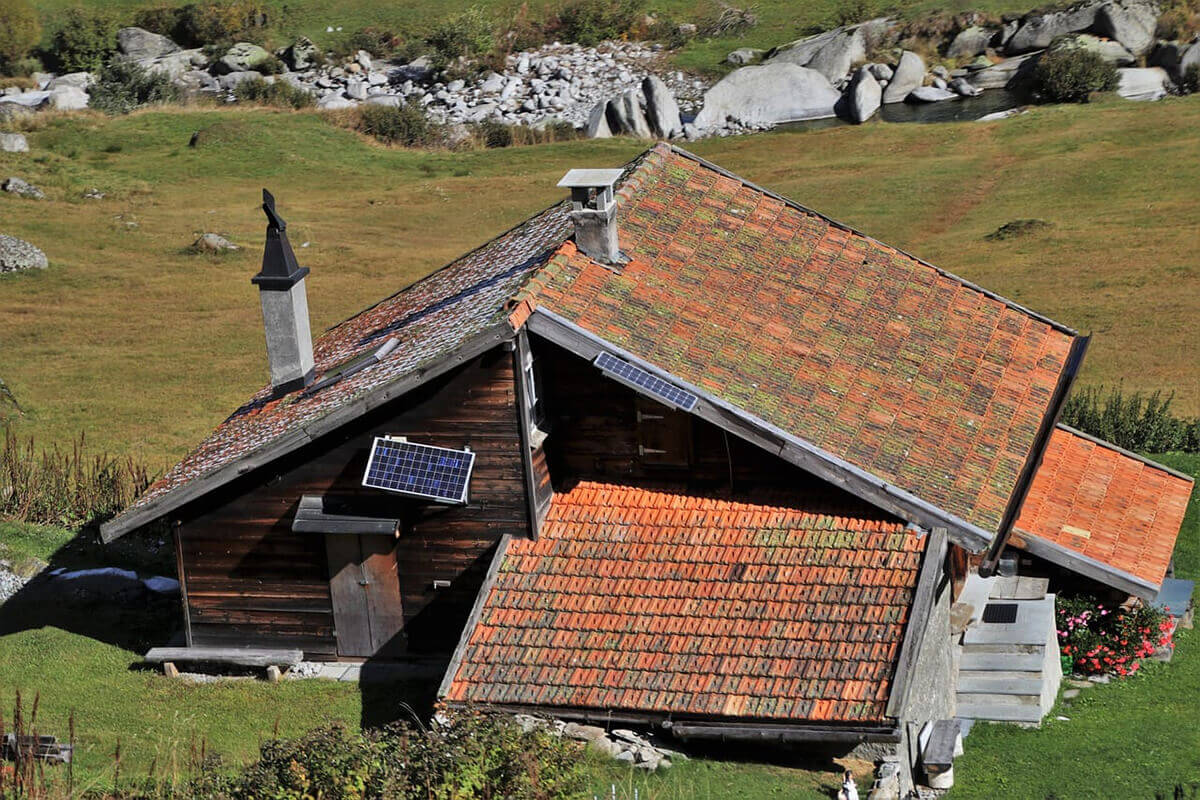
LiFePO4 also has industrial uses such as providing backup power to telecom towers or off-grid areas without access to a reliable grid connection.
Furthermore, these batteries can be utilized in uninterruptible power supplies (UPS) which prevent sudden shutdowns at critical moments by supplying emergency reserve power when needed. These UPS systems are commonly employed in data centers where valuable information must remain secure even under extreme conditions caused by blackouts or other disasters that cause disruption to a main supply.
Overall, LiFePO4 technology is an optimal choice for many types of applications thanks to its remarkable features including exceptional safety standards, extended cycle life and quick charging capabilities.
Its capacity for storing large amounts of energy with minimal degradation over time provides users with peace of mind knowing that their devices will remain powered even under the most demanding circumstances.
Factors Affecting Battery Performance And Lifespan
Lifepo4 batteries are composed of a variety of materials that must be carefully selected for their specific properties in order to ensure maximum performance and longevity. Several factors determine the overall quality and reliability of LiFePO4 cells, such as:
- Cell chemistry composition
- Raw material quality
- Manufacturing conditions
- Assembly methods
- Operating environment
Cell chemistry composition is an important factor since it affects the cell's energy density, rate capability and cycle life. In general, higher-grade raw materials significantly improve battery performance compared to lower-grade ones.
Proper manufacturing conditions also play a role in ensuring the proper functioning of cells; high temperatures can degrade electrode components while low temperatures may cause poor contact between electrodes and other parts.
Furthermore, assembly methods used during production affect the electrical characteristics of cells; improper assembly techniques could lead to reduced capacity or shortened lifespan.
Finally, the operating environment determines how well the battery performs over time; extreme temperature changes and exposure to moisture can reduce battery life expectancy. Therefore, all these elements need to be taken into consideration when selecting lifepo4 batteries for any application.
Storage Requirements For Lifepo4 Batteries
LiFePO4 batteries are becoming increasingly popular due to their advantages over other types of rechargeable batteries. However, the proper storage and handling of these batteries is critical for ensuring their optimal performance and long life. The following outlines some key considerations when storing LiFePO4 batteries.
The most important factor in preserving a LiFePO4 battery's efficacy is temperature control. Extreme temperatures can cause irreversible damage to the cells that make up the battery pack. For example, high temperatures will reduce cell capacity more quickly than low temperatures, potentially leading to premature failure if not properly managed.
It is therefore recommended that these cells be stored at an ambient temperature between 10-30 degrees Celsius (50-86 Fahrenheit). Additionally, it is important to avoid large fluctuations in temperature during storage as this may contribute to accelerated degradation of the cells.
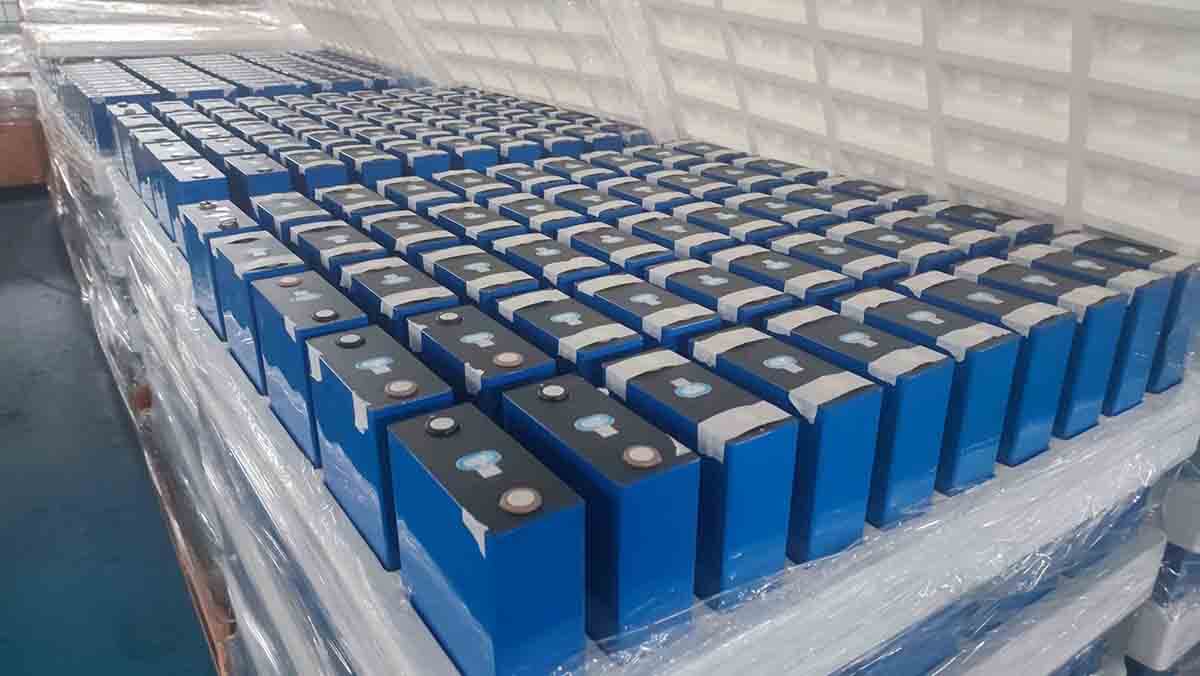
Humidity also plays a role in how well LiFePO4 batteries store energy and maintain their longevity. Cells should be kept away from excessive moisture or condensation which could lead to corrosion inside the cell structure and decrease overall capacity over time. This can be accomplished by maintaining relative humidity levels below 70%.
Furthermore, cells should always be sealed securely with no exposure to open air before being stored for extended periods of time; any contact with oxygen can hasten oxidation processes within the cells which would degrade their performance significantly faster than usual.
In order to ensure maximum efficiency from a LiFePO4 battery, manufacturers recommend regularly cycling them through charge/discharge cycles while they are in storage typically once every 3 months or so depending on usage patterns or environmental conditions.
In addition, periodic checks should be done on voltage levels throughout the lifespan of each cell since voltage drops may indicate greater problems such as shorted connections or faulty components within individual cells or packs themselves. With proper care taken during storage and regular maintenance conducted afterward, LiFePO4 batteries will remain reliable sources of power for many years into the future.
Recycling Lifepo4 Batteries
Recycling LiFePO4 batteries is an important part of responsible battery use. Recycled components can be used to make new batteries, reducing the need for raw materials and helping to reduce environmental impact. By recycling these batteries we can help conserve resources and protect our planet’s environment.
The process of recycling LiFePO4 cells starts with dismantling the battery into its component parts. This includes collecting all individual cells, separators, terminals, packaging material, etc., which are then separated into different categories based on their composition.
The metals contained in the cells are extracted and treated separately from other materials such as plastics or rubber compounds. The recovered precious metals are further processed through smelting operations that produce pure metal ingots while non-metals undergo thermal decomposition into a liquid form that can later be recycled as feedstock for molding processes.
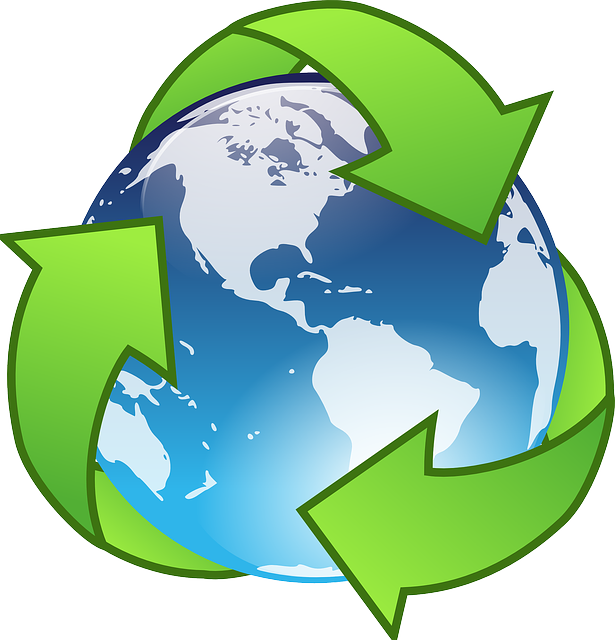
By using this method, around 95% of the original cell mass can be reused in some way or another, making it very efficient compared to traditional recycling methods like burning or burying them in landfills.
Furthermore, it provides us with a more sustainable option than mining virgin ore deposits for rare earth elements found in many modern lithium-ion batteries. This technology has been developed over several decades and continues to evolve as industry standards become increasingly stringent regarding waste management and product lifecycle considerations.
Safety Considerations When Working With Lithium-Ion Batteries
The safety of LiFePO4 batteries must be taken into account when working with them. Manufacturers of LiFePO4 cells have developed detailed protocols for the safe use, storage and disposal of these cells. It is important to follow this guidance from manufacturers in order to ensure that LiFePO4 cells are not mishandled, stored incorrectly or handled unsafely during their lifetime.
Potential Hazards | Mitigation Strategies | Additional Resources |
---|---|---|
Fire Risk | Use Thermal Management Systems (TMS) | UL Standards 6800B & 1642C IEC/EN 62133 UL 2054 Standard for Batteries Used In Stationary Power Applications |
Overcharging | Utilise Battery Monitoring Systems (BMS) | IEEE 1547 Standard SAE J1772 Charge Coupler Interface Requirements |
Short Circuit | Ensure a Properly Designed Cell Pack System | IPC/JEDEC JESD 95A Specification ISO 13485 Quality Management System |
Following manufacturer guidelines can reduce the risk associated with handling, storing and disposing of lithium ion batteries significantly.
Furthermore, there are several standards and quality management systems available that provide additional requirements on the design, assembly and testing processes used by battery pack suppliers as well as end users.
- These standards include:
- UL Standards 6800B & 1642C for thermal management systems; IEC/ EN 62133 for rechargeable batteries.
- UL 2054 Standard for Batteries Used In Stationary Power Applications.
- IEEE 1547 Standard regarding charge couplers.
- SAE J1772 Charge Coupler Interface Requirements.
- IPC/JEDEC JESD 95A specification on cell packs system design and ISO 13485 Quality Management System related to medical device design and manufacturing process.
By adhering to these standards it is possible to minimize potential hazards while ensuring the proper operation of LiFePO4 cells over time.
Future Developments In Lifepo4 Battery Technology
The future of LiFePO4 battery technology is an area of intense research and development. The ability to store larger amounts of energy, increase cycle life, improve safety, reduce cost and decrease environmental impact are all areas where significant advancements can be made in the near future.
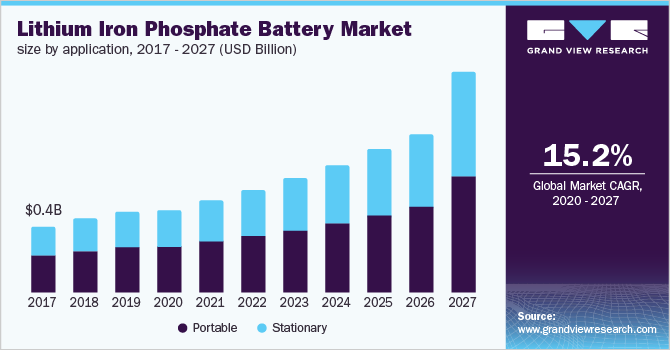
One promising avenue for advancement is nanotechnology. By utilizing nano-materials such as carbon nanotubes or graphene, it may be possible to create batteries with increased power density, higher specific energy storage capacity and improved durability over current designs. This could lead to lightweight portable batteries that can charge faster and last longer than traditional lithium ion cells.
Another potential area of improvement lies in the use of novel electrolytes. Novel electrolyte formulations have been proposed which show promise towards further improving cycle life while also increasing temperature tolerance range. Additionally, there are several emerging technologies that aim to reduce materials costs by using alternative cell architectures such as pouch cells or prismatic cells instead of cylindrical formats currently used in production commercial applications.
These developments present exciting opportunities for both industry players and scientists alike:
- Increased power density and specific energy storage capabilities
- Improved cycle life through new electrolyte formulations
- Potential reduction in material costs due to novel cell architectures
- Faster charging times enabled by nano-materials
- Greater temperature operating range combined with improved safety features
It remains to be seen how much progress will be made on these fronts but one thing is certain - LiFePO4 batteries continue to offer a viable solution for many large-scale stationary energy storage needs alongside smaller consumer electronics applications.
Conclusion
The development and manufacture of LiFePO4 batteries has come a long way since they first entered the market. These advanced battery systems have changed the face of lithium-ion technology and are now considered one of, if not the most reliable battery system available on the market today.
The assembly process is highly precise, with each individual cell undergoing multiple stages during manufacturing to ensure top-quality performance and safety standards. In addition, these cells must meet rigorous storage requirements in order to maintain effectiveness over time. Finally, recycling processes for worn-out or damaged batteries ensure that resources are being reused efficiently and responsibly.
In conclusion, LiFePO4 batteries represent an incredible milestone in energy storage technology due to their reliability, efficiency, and environmental friendliness.
With ongoing research into new materials suitable for use in this type of battery system as well as improved production techniques, we can only expect further advances in power density, cycle life expectancy, cost savings, and more importantly - safety measures taken by manufacturers when producing such powerful devices.
It is truly remarkable how much progress we have made in just a few short decades, making LiFePO4 batteries an excellent choice for those looking for a dependable source of energy storage solutions.