Preventing Catastrophe: Top BMS Failure Problems & Solutions
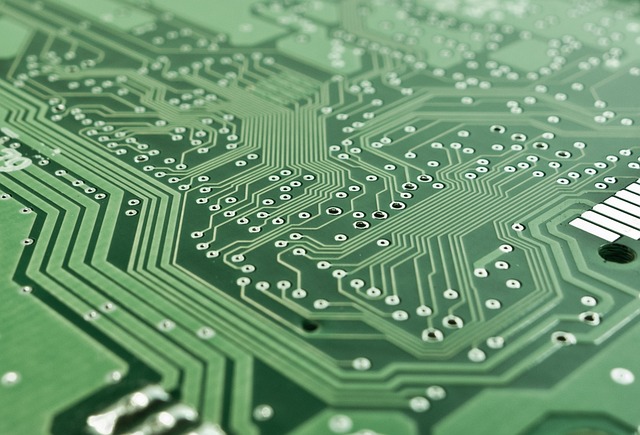
Battery management systems (BMSs) are critical components in modern technology. They enable us to store and control energy, allowing us to power our phones, laptops, and other devices. Without reliable BMSs that function properly, these pieces of equipment would no longer be able to operate as intended. Unfortunately, BMSs can fail due to a variety of reasons. In this article, I'll discuss 5 common battery management system failure problems and their solutions.
Harveypower as a manufacturer in the field of energy storage systems for many years, we know from first-hand experience how important it is for any device that uses a battery management system to have a system that is always up - especially when it comes to safety-critical situations such as electric vehicles or medical equipment! Fortunately, understanding why these failures occur and what you can do to prevent them can help ensure the long-term reliability and performance of your equipment.
This article will provide readers with an overview of the most common problems associated with BMS failure along with practical advice on how they can diagnose and resolve those issues quickly and effectively. So if you want to gain greater insight into the world of battery management systems and understand how best to keep yours running optimally at all times - then read on!
Overview Of BMSs
Battery Management Systems (BMSs) are specialized systems designed to monitor and control the charging, discharging, cycling and other aspects of batteries. They're essential components of most battery-powered devices, from smartphones to electric vehicles.
The main purpose of a BMS is to protect the battery from damage due to overcharging, over-discharging, or any other kind of misuse that can cause permanent harm. A good BMS will also actively manage how energy flows in and out of the battery for optimal performance and life span. It does this by monitoring various parameters such as voltage levels, temperature fluctuations, current flow direction and more.
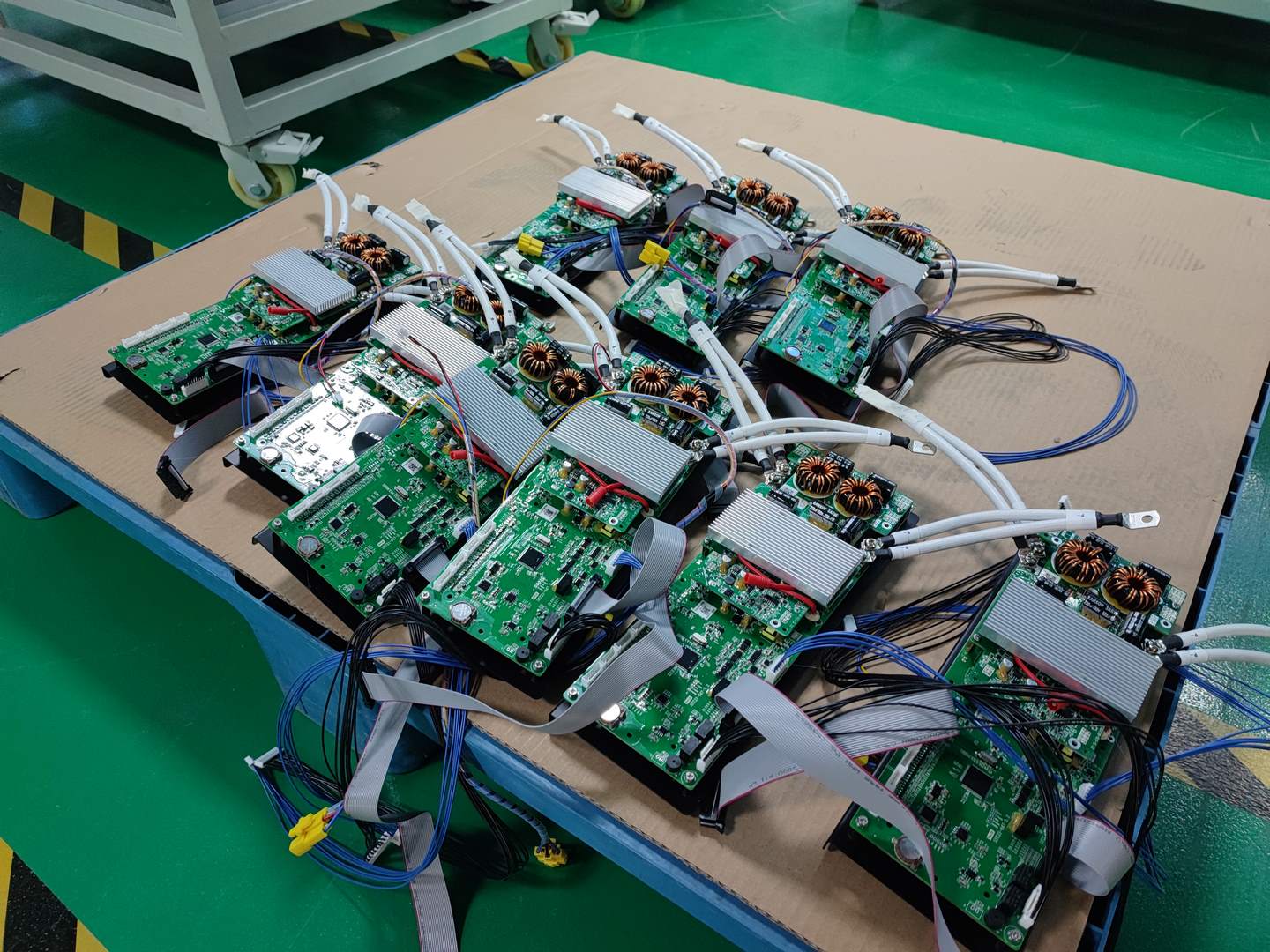
To ensure the proper functioning of a BMS it's important to keep all its components working correctly from hardware like circuit boards and sensors to software like algorithms and communication protocols. Regular maintenance should be carried out periodically to check for signs of wear or malfunctioning parts so that issues can be identified early on before they become bigger problems down the line.
With regular preventive care, you can keep your BMS running smoothly and help avoid costly repairs or replacements. To wrap up, having an efficient Battery Management System is key to ensuring the safe operation of your device while optimizing battery performance at the same time.
Causes Of BMS Failure
Common causes of battery management system failure include cell imbalance, overcharging and undercharging, temperature-related issues, and communication errors.
Reason | Malfunction |
Cell Imbalance | Cell imbalance is a common issue that can arise due to differences in the individual cells' capacities or charge levels. This can lead to an overall power drain on the BMS as well as accelerated aging of some cells over others. |
Overcharging | Overcharging occurs when voltage exceeds the maximum safe level for charging and can cause permanent damage to the BMS. |
Undercharging | Undercharging happens when voltage drops below the minimum threshold required for the proper operation which can result in reduced the lithium battery cycle life and capacity fade. |
Temperature-related Issues | Temperature extremes will also have an impact on performance by causing increased resistance within components leading to circuit failures, weakened insulation, and corrosion of contacts. |
Communication Errors | Lastly, communication errors between modules are often caused by faulty wiring connections or incorrect programming settings which may hinder efficient monitoring and control of a BMS’s operations. |
In order to reduce these potential problems it's important to ensure that all parts are properly installed with quality materials, use appropriate protective equipment where necessary, maintain accurate records of system parameters and live readings during maintenance checks, replace any malfunctioning component quickly, keep temperatures within operating range limits at all times, and employ experienced personnel who understand how each component works together in harmony.
Cells Overcharging
When a battery management system fails, cell overcharging can be one of the primary causes. Overcharging prevention measures must be in place to protect against this risk. It is important to ensure that your BMS has features such as overcharge detection and monitoring functionality so it can detect any cell overcharges early on and prevent them from occurring or escalating.
The most common cause of cell overcharging is when the charge current exceeds the maximum allowable rate for the cells being charged. This results in an excessive voltage buildup within each individual cell, leading to accelerated aging and ultimately reducing its capacity.
In addition, if left unchecked, high temperatures may result due to increased internal resistance which could damage the cells permanently.
Other factors like faulty wiring and incorrect programming settings can also contribute to cell overcharging situations.
It is imperative for a BMS to have proper safety mechanisms in place to effectively monitor and control charging conditions before they become hazardous. These include setting appropriate temperature thresholds, limiting charge currents, implementing low-voltage cutoffs, providing accurate charge algorithms, and using active balancing techniques between cells where necessary.
By taking proactive steps with these solutions, you can help ensure that all cells are protected from potential dangers associated with overcharging incidents.
Cells Undercharging
It is a common misconception that cells are undercharging when BMSs failure or malfunction occurs. But in truth, the likelihood of cells being undercharged as a result of such failures is slim. It’s more likely an issue with connectivity between the battery and management system than anything else.
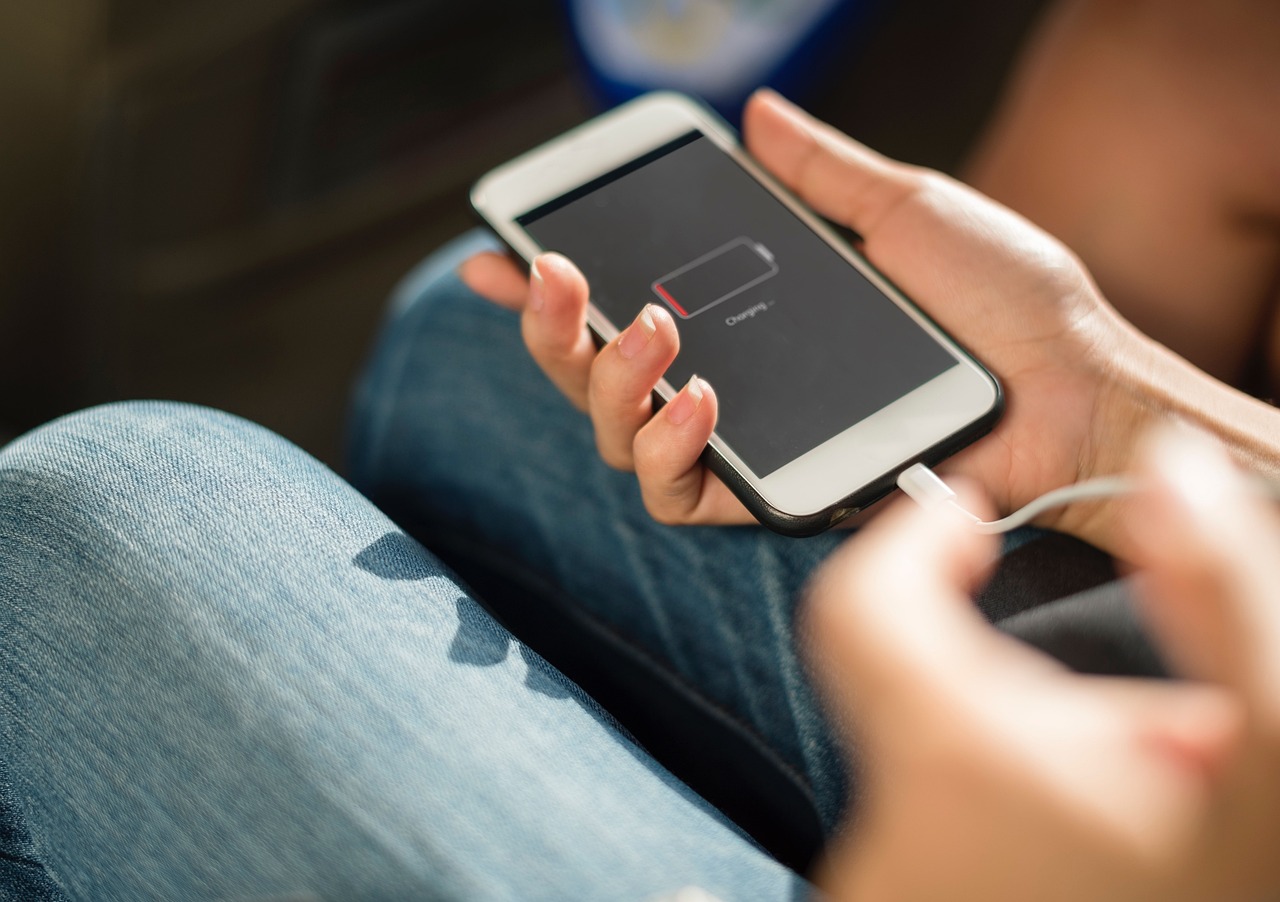
So what can be done if there are indeed undercharged cells? The first step would be to identify which cell(s) has failed and why—whether it’s low voltage due to poor connection, a damaged terminal, etc. After a thorough inspection of all components involved, one should then assess whether any action needs to be taken on the underlying cause. Such actions may include replacing faulty equipment or cleaning contacts for better conductivity.
Once corrective measures have been implemented, the next course of action is to recharge the affected cell(s). This process involves carefully monitoring their charge level throughout and ensuring they don’t get overcharged either. Doing so will help avoid further damage from occurring and ensure your battery remains healthy for longer periods of time.
Voltage Imbalance Between Cells
Voltage imbalance between cells can be one of the most challenging problems to diagnose and prevent in a battery management system. It occurs when there is an unequal distribution of cell voltages, resulting in a difference greater than certain thresholds specified by the manufacturer. This voltage imbalance can cause significant consequences, including reduced performance and efficiency, increased degradation rates, and even catastrophic battery failure.
To mitigate these risks, it's essential that you have strategies for diagnosing and preventing voltage imbalances between your cells. The first step is to measure each cell’s individual voltage regularly and compare them against the upper and lower limits set by the BMS manufacturer. If any readings fall outside these thresholds then action must be taken immediately based on the severity of the deviation.
The second important factor in managing cell-voltage imbalances is prevention through proper design considerations such as ensuring all components are correctly sized for their application, using high-quality materials, providing sufficient cooling capacity for both active and passive elements of the system, and testing thoroughly throughout the development cycles.
By implementing these practices at every stage from conception to production, you'll increase safety margins while decreasing the risk of dangerous situations arising due to voltage imbalance issues.
Overheating
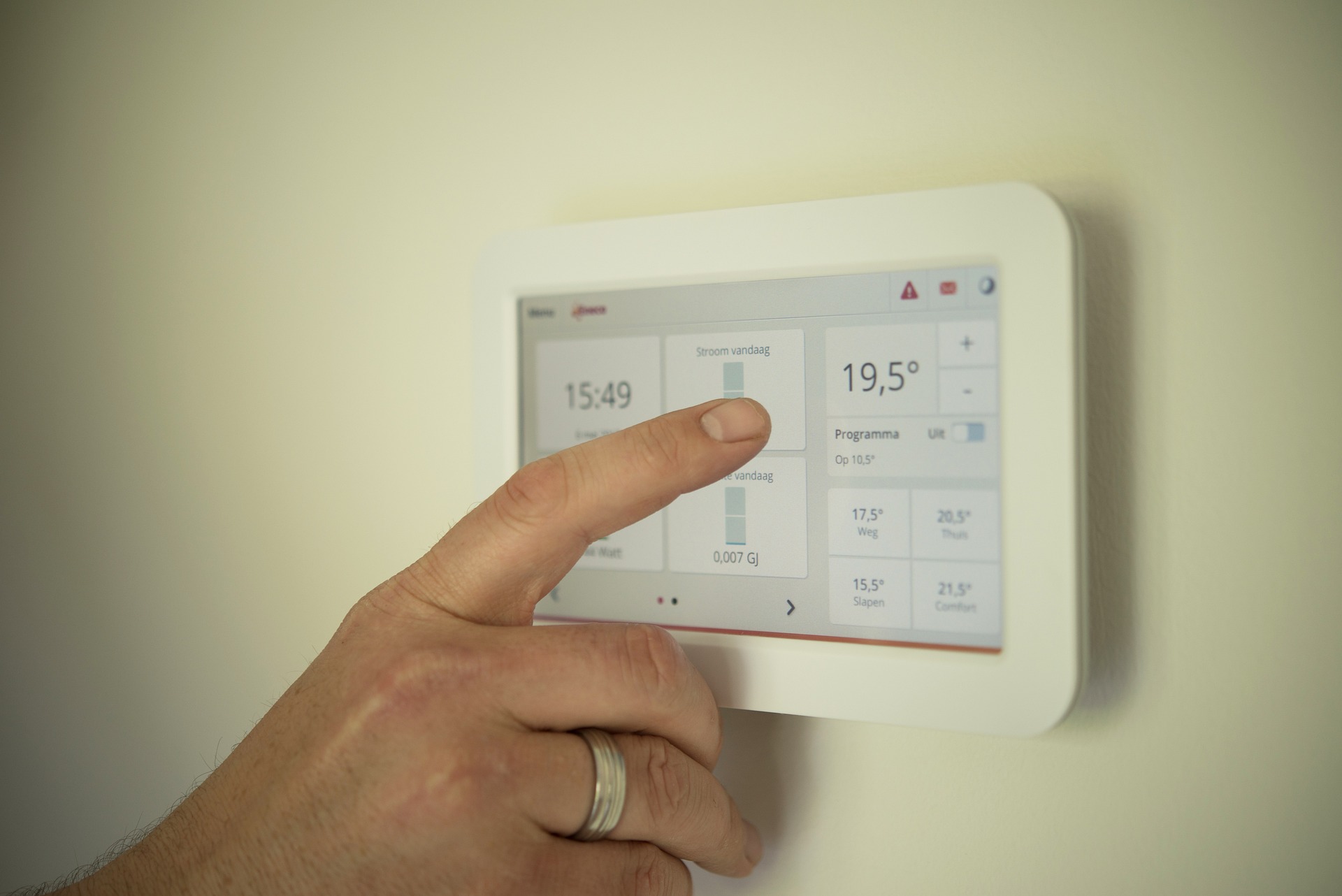
The temperature of a battery management system can be one of the most volatile elements in its operation. It is like an inferno, raging and waiting to consume any weakness that stands in its way. As such, preventing overheating is essential for optimal performance and longevity. Temperature monitoring should be implemented throughout the entire system; this will ensure that heat control mechanisms kick into action at the right times.
Thermal management strategies are key when it comes to controlling excessive temperatures. Battery cooling solutions including airflow systems, liquid coolants and insulation materials are all very effective tools for maintaining ideal operating conditions within a BMS environment. Furthermore, these measures need to be monitored carefully over time as environmental changes may have an impact on their effectiveness.
Overall, prevention is better than cure when it comes to managing high temperatures within a battery management system. Having robust thermal management strategies in place from the get-go will go a long way toward helping maintain peak performance while avoiding costly repairs down the line due to damage caused by excess heat levels. Taking proactive steps now allows you to gain greater control over your BMS's performance today and into the future.
Poor Cell Quality Control
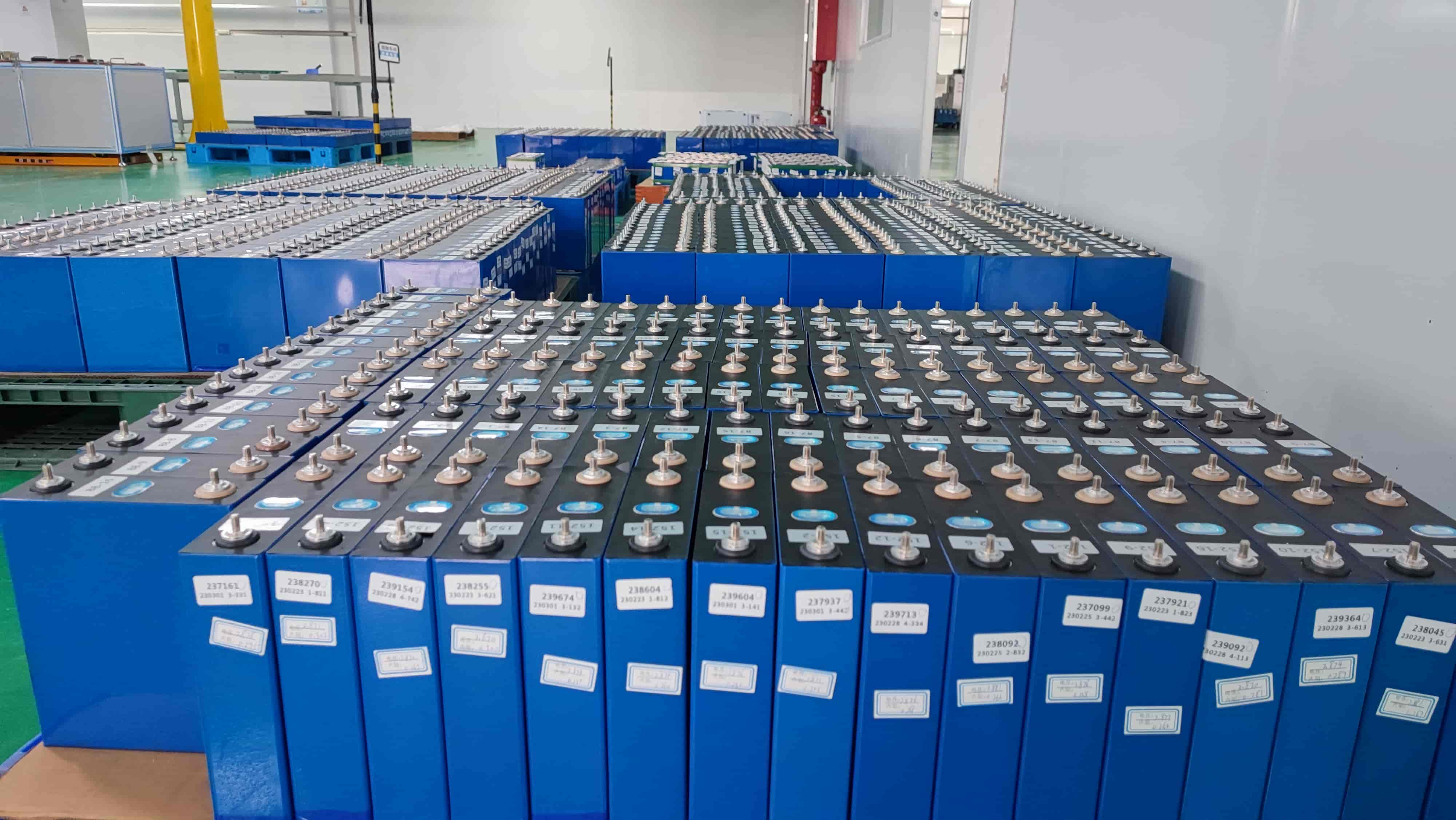
Poor cell quality control is a critical issue in battery management systems. Cell manufacturing defects, as well as improper use of cells, can lead to catastrophic failures and premature aging. To avoid such issues, proper quality control procedures must be implemented during each stage of the system's life cycle. This includes rigorous inspection at the time of installation, periodic maintenance checks, and accurate diagnostics when necessary.
Cell monitoring technology plays an important role in ensuring that cells remain functional in the long run. It monitors performance parameters like voltage, resistance, temperature, etc., which are essential for reliable operation. By tracking these values over time, potential problems can be identified before they become major issues. In addition to this, it also helps in detecting any abnormalities due to internal or external factors that could affect cell performance and cause damage to the system components.
To prevent poor-cell-quality-control-related failure problems from occurring, manufacturers need to ensure strict adherence to their quality-control procedures by using advanced cell-monitoring technology for accurate diagnostics. This will help them identify emerging faults quickly and take corrective measures accordingly so that the overall efficiency of their systems remains intact.
Temperature Sensing Problems
Like a firefighter inspecting the scene of an accident, one must identify and address underlying thermal sensing issues to prevent further damage. In battery management systems (BMS), temperature sensing is especially important for accurate monitoring and overall system health. Here are three key areas of focus when troubleshooting temperature-sensing problems:
- Evaluating sensor accuracy
- Analyzing voltage readings
- Identifying proper grounding techniques
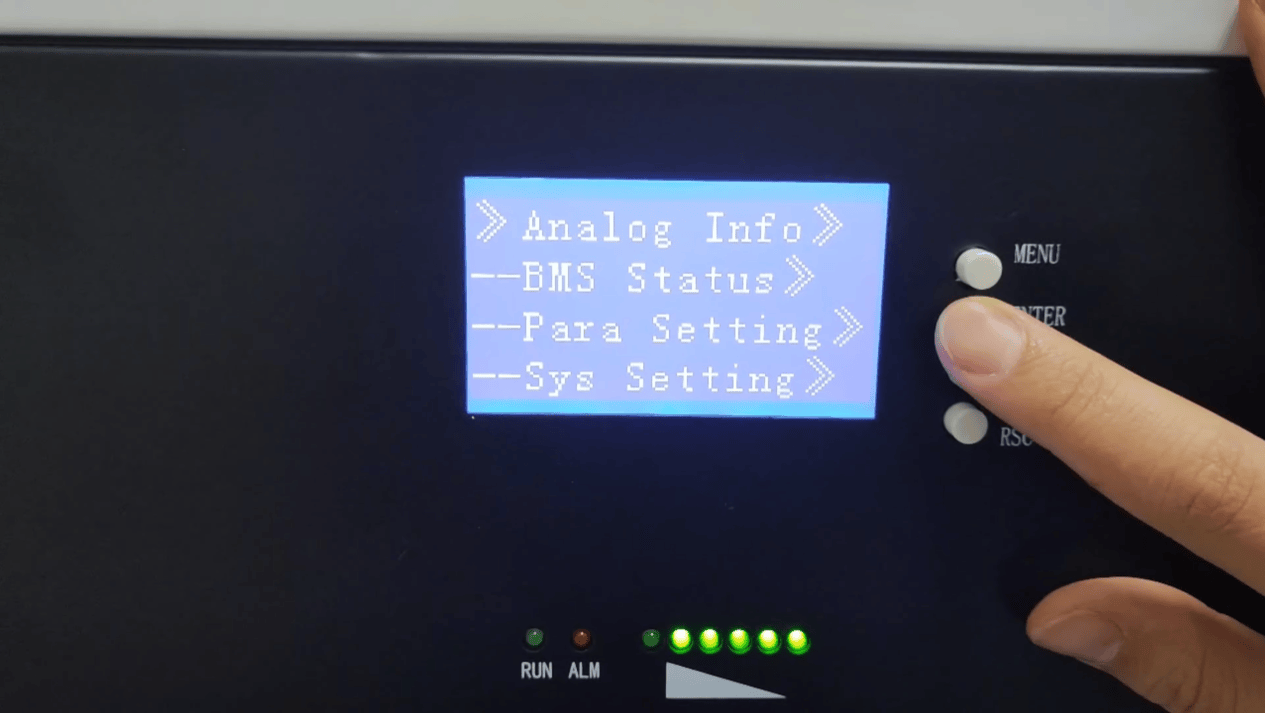
It's essential to assess the accuracy of temperature sensors before attempting any other fixes. If BMS operations depend on accurate thermostat readings then faulty sensors can lead to major malfunctions or even catastrophic failure down the road. A technician should always check voltages during inspections as well; if they don't match up with expected values then there could be a deeper issue at hand. Finally, improper ground connections may also cause heat detection failures so it's best to ensure that all cables are properly connected according to safety protocols.
In addition to these core solutions, technicians should employ advanced diagnostic tools such as infrared imaging cameras and thermistors in order to pinpoint specific temperature-sensing errors. By utilizing these instruments in conjunction with traditional problem-solving strategies, one can effectively diagnose and repair complex thermal sensing issues in record time. With the right combination of skills and knowledge, any BMS expert can restore normal operations quickly and safely - no matter how severe the malfunction might seem!
Communication Issues
Communication issues are often the primary cause of battery management system failure. Poor or faulty connections between batteries, as well as communication errors due to incompatibility with hardware and/or software can lead to connectivity problems that prevent proper operation. It is essential that these communications protocols are in place prior to the installation and setup of any BMS components. This will ensure compatibility throughout all aspects of the system, allowing for proper functioning at all times.
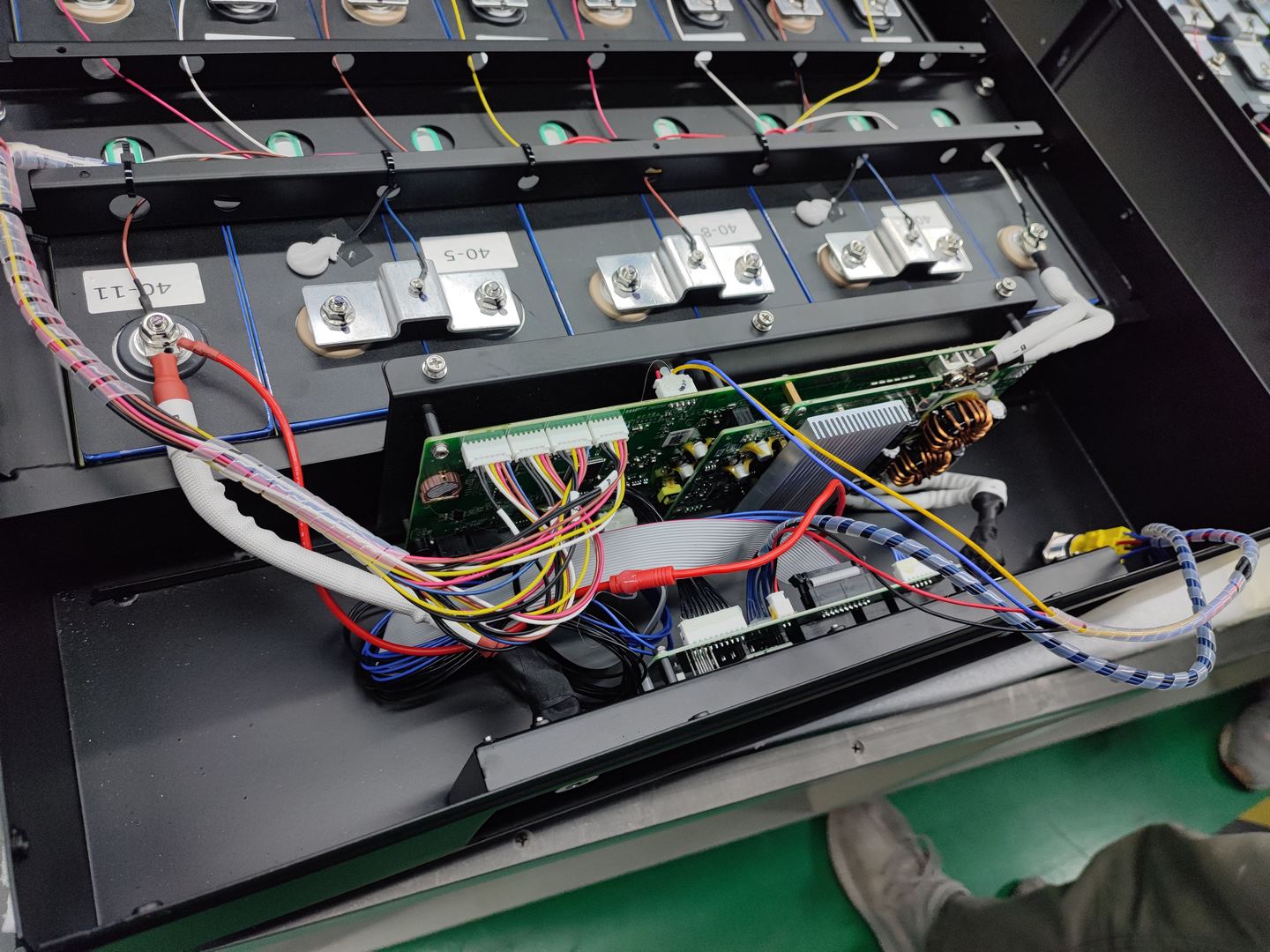
If a communication issue arises during use, it may be necessary to troubleshoot by first checking connection points on each component. If there appears to be no physical problem, then replacing individual parts such as sensors or wiring harnesses could help fix the problem. In some cases, however, an entire new BMS might have to be purchased if communication-related malfunctions persist despite other attempts at resolution.
Ultimately, communicating effectively between batteries and the main control unit is key for the seamless operation of a battery management system. Attention must therefore be paid when setting up the system so that potential communication issues do not occur down the road. With the careful implementation from initial development through full deployment, users should experience minimal disruption from their BMS - enabling them to enjoy more reliable results every time they use it.
Battery State Estimation Error
Battery state estimation errors are a common issue in battery management systems. They occur when the system is unable to accurately determine the current state of charge (SOC) or other important data points of a battery. This can lead to incorrect control decisions that cause the system to incorrectly power down, shut off, or otherwise fail to operate correctly. Fortunately, there are several solutions available for addressing this type of error and ensuring optimal performance from a BMS.
One solution involves using advanced algorithms such as adaptive filters and Kalman Filters which allow for more accurate predictions of SOC and other important parameters. These algorithms also provide better accuracy than traditional methods such as linear extrapolation or least-squares fitting. Another effective method is to use signal processing techniques like Fourier transforms which improve the precision of measurements by removing noise from signals. Finally, implementing redundancy into state estimations provides additional protection against potential errors due to factors like environmental conditions or aging effects on batteries.
In order to ensure reliable operation from a battery management system it is crucial to properly address any issues related to batter state estimation error. Advanced algorithms and signal processing techniques offer an effective way of doing so while redundancy helps protect against unexpected changes in the environment or aging effects on batteries. By following these steps, you can reduce the risk of failure and maintain optimal performance from your BMS.
Maintenance And Troubleshooting Strategies
Maintenance and troubleshooting of a battery management system (BMS) can be akin to an art form one must capture the nuances while executing preventative measures with precision. But, when done right, it is often the difference between success and failure. Below are some strategies for ensuring that your BMS remains in optimal condition.
Maintenance | Troubleshooting |
---|---|
Battery Maintenance | State Estimation Strategies |
Sensor Maintenance | Software Upgrades |
Preventative Measures | Voltage & Current Monitoring |
To keep your BMS functioning correctly, regular maintenance should be performed on both the batteries themselves as well as the sensors responsible for gathering data from them. This involves checking for any signs of physical damage or degradation such as corrosion or frayed wires, testing performance levels, inspecting connections and replacing faulty components if necessary. Additionally, preventive measures like cleaning terminals and regularly monitoring voltage/current levels should also be taken into consideration.
When it comes to troubleshooting, state estimation strategies are essential for accurately diagnosing potential problems within a BMS system. The process involves using algorithms to estimate the current state of certain components based on input from various sensors over time. If discrepancies arise then further investigation may be required to pinpoint any issues before taking corrective action.
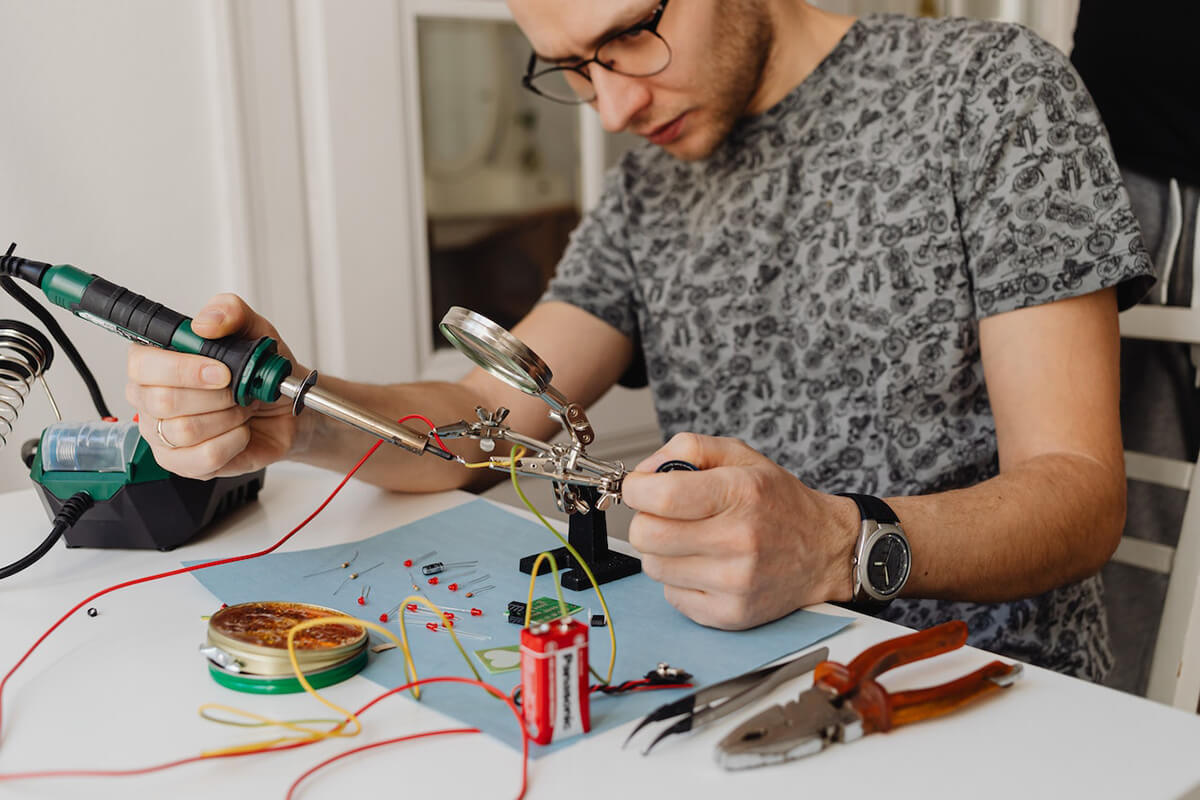
Other common approaches include software upgrades which allow for more efficient use of resources along with improved fault detection capabilities; and voltage/current monitoring which helps identify possible overloads due to misalignment or other anomalies related to power distribution networks.
Adopting these practices not only ensures longevity but also provides peace of mind knowing that you will have access to real-time information regarding your battery management systems health status at all times - giving you control when unexpected circumstances arise.
Safety Procedures For Working With Batteries
Having discussed maintenance and troubleshooting strategies, it is now time to discuss safety procedures for working with batteries. Working with a battery management system requires the utmost caution in order to ensure a safe environment. It's essential that you understand proper battery handling protocols when dealing with any type of battery, particularly those used in BMSs.
When handling batteries, always wear protective gear such as gloves and eyewear. If a battery should spill or leak during use, be sure to clean up the area immediately and dispose of any debris safely away from your workstation. Never touch exposed terminals on any kind of battery; doing so could result in serious injury or even death due to electrical shock.
When charging batteries, make sure they are adequately ventilated and far away from flammable materials. Monitor their temperature constantly while checking regularly for signs of overheating or swelling which can indicate an impending failure.
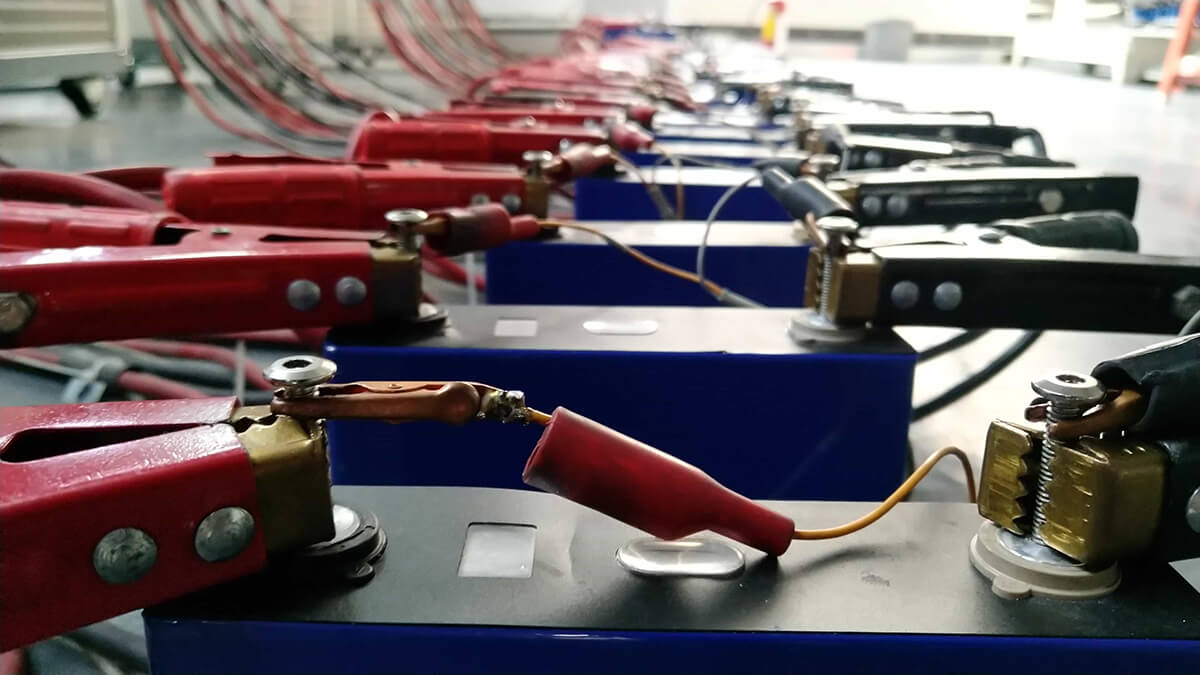
It is also important to remember that no two types of batteries are alike and require different levels of care when being handled or serviced. Always consult the manufacturer’s instructions before operating or servicing a new set of batteries to ensure you know how best to care for them in accordance with current regulations and standards. With these steps followed carefully, you can ensure that both you and your equipment remain safe while working with batteries!
Preventative Measures To Avoid Failures
"An ounce of prevention is worth a pound of cure," goes the old adage. This rings especially true when it comes to battery management system failures, as certain preventative measures can help avoid any issues before they arise. To make sure your BMS remains in optimal condition and continues running efficiently, here are 3 key steps you should take:
- Monitor cell quality - Ensure that all cells have a consistent performance by regularly monitoring their individual performances with voltage tests and other methods. Doing this will allow users to spot potential problems early on and take corrective action if needed.
- Temperature sense - Make sure temperature sensors are installed in strategic locations within the battery pack so that fluctuations can be detected quickly and dealt with accordingly. By doing this, thermal runaway conditions can be avoided which may otherwise cause catastrophic failure of the entire system.
- Communication issues - Proper communication between components is essential for the smooth operation of the BMS and must be checked routinely throughout its usage period. Any anomalies or errors must be addressed immediately to ensure no disruption or malfunction occurs over time.
These three points form an important foundation for maintaining a healthy battery management system free from any major failure risks. Furthermore, regular maintenance checks should also be conducted according to manufacturer guidelines to keep everything running optimally at all times. Taking these simple preventive measures now can save you significant headaches down the road!
Software Solutions
Now that preventative measures have been discussed, software solutions should also be considered when it comes to avoiding battery management system failure. BMSs (battery management systems) are sophisticated machines, and the proper software can help keep them running smoothly. Software solutions tailored specifically for battery management can monitor and diagnose any potential issues before they become full-blown failures, providing an extra layer of protection against costly repairs or replacements.
One example of a software solution is BMSS software, which stands for Battery Management System Software. This program provides real-time monitoring and diagnostic capabilities so you can identify problems early on and take corrective action as needed. It allows users to set thresholds for various parameters such as voltage, temperature, SOC (state of charge), SOH (state of health), etc., enabling better control over the system's performance.
In addition, the data collected by this software gives valuable insight into the overall state of your battery pack, allowing you to make informed decisions about maintenance schedules and other important aspects of your battery management plan.
Software solutions like these provide an efficient way to ensure safety and reliability in a variety of applications where batteries are used. By using advanced analytics combined with predictive algorithms, these programs can alert you if anything goes wrong with your equipment and give you enough time to rectify the issue before it becomes too serious.
With proactive monitoring tools at your disposal, you’ll always have access to reliable information about your battery packs—giving you peace of mind knowing that everything is running smoothly.
Hardware Solutions
Common BMS hardware failure problems can be difficult to diagnose, but solutions are available. One of the most frequent causes of the malfunction is a faulty protection circuit that fails to shut off power when it reaches unsafe levels. A reliable monitoring system should have an independent balancing circuit for each battery cell, which will monitor and regulate its charge simultaneously. This helps maintain uniformity across all cells in the pack, ensuring maximum performance from the entire system.
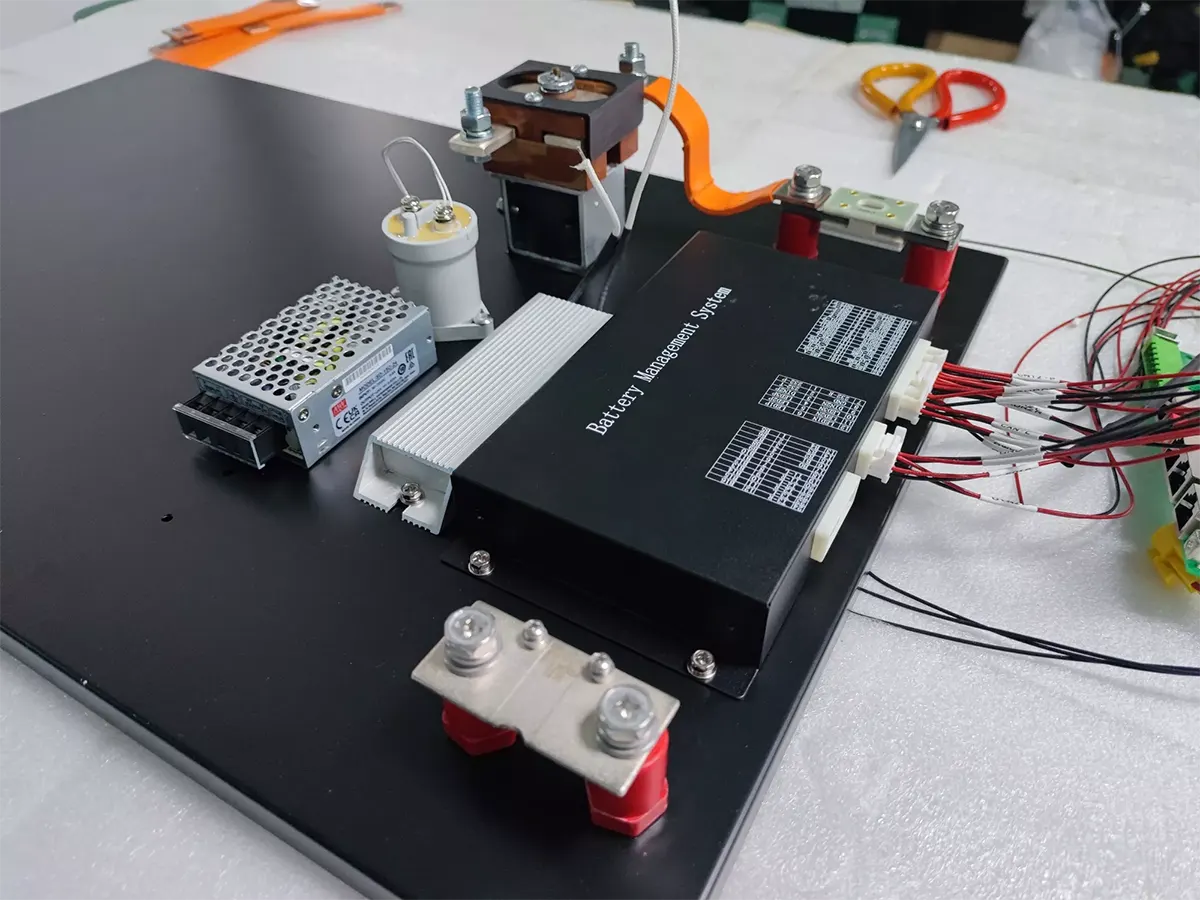
Another common problem is incorrect installation or wiring errors that lead to improper operation of the BMS hardware components. Incorrectly wired connection points between components can cause intermittent failures or complete shutdowns, resulting in poor performance and potential safety risks due to exposed live wires. The best way to prevent these issues is by following manufacturer-recommended wiring diagrams carefully and using high-quality electrical connectors with adequate insulation properties.
Good maintenance practices are also essential for avoiding BMS hardware problems. Periodic checks on connections and terminals help detect any signs of wear or corrosion before they become serious enough to affect functionality. Taking proactive steps such as replacing worn parts regularly helps ensure safe operation and long life from your battery management system components.
Conclusion
Knowing common BMS failure issues and solutions is essential knowledge for anyone working with batteries. Identifying the cause of failure to avoid failure and important safety procedures when working with batteries are essential. What's more, it's crucial to take preventive measures before anything goes wrong so that you don't have to worry about a possible disaster later on.
Finally, software and hardware solutions provide us with the tools we need to spot warning signs early and implement corrective action quickly all while keeping our batteries safe from damage or destruction due to inadequate maintenance. With these tips at your disposal, you'll be able to keep your battery running smoothly for years!
So if you're serious about protecting your valuable investments and preserving their longevity, make sure you review this list of common BMS failures regularly after all, prevention is always better than cure!