Wat is het Battery Management System Solar? (Complete gids)
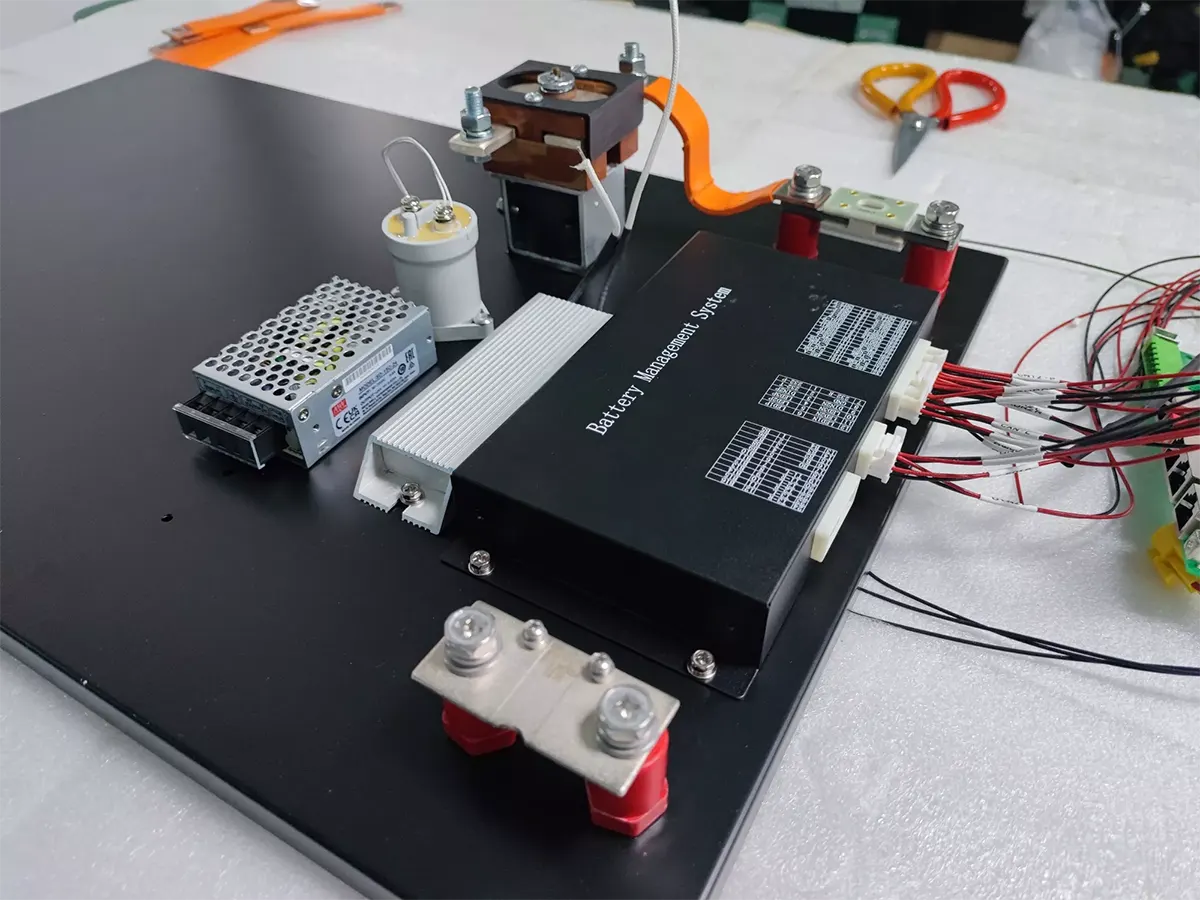
Battery management system solar exterior structure and wiring connection
We are fortunate to live in an era of advanced technology and enjoy the surprises brought by high technology. But now high technology is often inseparable from power support. And large battery arrays can be used as energy storage systems for backup and continuous power supply - energy storage batteries, so this usage is getting more and more attention.
At present, the most used energy storage battery should be the lifepo4 battery. For an energy storage battery pack, a fully functional BMS management system is very important, which can improve the efficiency of the energy storage battery pack. Give full play to it.
In this article, I will list the functions and types of BMS systems in detail. Let everyone better understand the importance of BMS. Pay attention to the safety regulations of energy storage battery applications in households or industries.
What is A BMS?
The general name of BMS is Battery Management System, which is a control system to protect the safety of battery use. It is mainly for intelligent management and maintenance of each battery unit, to prevent overcharging and over-discharging of the battery, to prolong the service life of the battery, and to monitor the status of the battery.
The BMS battery management system unit includes a BMS battery management system, a control module, a display module, a wireless communication module, electrical equipment, a battery pack for powering electrical equipment, and a collection module for collecting battery information of the battery pack.
BMS System Structure
(1) Mainboard
Collect the sampling information of each slave board, communicate with the battery through the interface, control the relay action in the BDU, monitor the various states of the battery, and ensure the safe use of the battery during charging and discharging.
(2) Slave board
Monitor the module’s cell voltage, cell temperature and other information, and transmit the information to the main board, with a battery balancing function. The communication mode between the slave board and the main board is usually CAN communication/RS232/RS485.
(3) BDU
Connected to the high-voltage load of the vehicle and the fast charging harness through the high-voltage electrical interface, including the pre-charging circuit, total positive relay, total negative relay, fast charging relay, etc., controlled by the main board.
(4) High-voltage control board
It can be integrated into the main board, or it can be independent. It monitors the voltage and current of the battery pack in real-time and also includes pre-charge detection and insulation detection functions.
The 4 Core Functions of Battery Management System Solar
1. Measurement function
It can measure the voltage and temperature of the single cell in real-time, and measure the terminal voltage and current of the battery pack and other parameters. To ensure the safe, reliable and stable operation of the battery, the guarantee
The service life requirements of the whole battery meet the requirements for optimal control of the operation of the single battery and the battery pack.
Ideal for stationary and mobile use from thousands of watts to hundreds of kW of power, battery-based backup power supplies can reliably and efficiently power a variety of uses.
2. Online SOC diagnosis function
On the basis of real-time data collection, an expert mathematical analysis and diagnosis model is established to measure the remaining power SOC of the battery online. The remaining battery capacity and reliable use time under the following.
There are many challenges in implementing a battery management system for energy storage applications, and the solution is by no means simply "scaling" from the management system of a small, lower-capacity battery pack. Instead, new, more complex strategies and key supporting components are required.
3. Battery system operation alarm function
When the battery system is in over voltage, under voltage, over current, high temperature, low temperature, communication abnormality, BMS abnormality, etc., it can display and upload, report alarm information.
The starting point of the challenge is that the measured values of many battery parameters are required to have high accuracy and reliability. (You can read about "How to Test the actual capacity of the Battery")
Furthermore, the planning of the subsystems must be modular to enable the configuration to be tailored to the specific needs of the user, taking into account possible expansion requirements, overall management issues, and necessary maintenance.
4. Battery system protection function
For abnormal fault conditions such as serious over voltage, under voltage, or over current (short circuit) of the battery that may occur during operation, the high voltage control unit realizes fast
Cut off the battery circuit quickly, isolate the fault point, and output sound and light alarm information in time to ensure the safety and operation of the system.
The Types of BMS
Topology is very important for BMS because it will affect the system cost, reliability, convenience of installation and maintenance, and accuracy of measurement prediction. From the perspective of topology, BMS can be divided into four types: centralized, modular, master-slave, and distributed according to different project requirements.
(1) Centralized
Centralized, also called integrated. It is to package the entire BMS in a device and throw out the wires to connect to the conductor battery.
Advantage:
- Compact structure, often just a box.
- Then the price is also cheaper.
- The maintenance is relatively simple, and it is often enough to replace the whole.
Disadvantage:
- The scalability is poor. If a product is finalized and wants to be expanded, it has to be redesigned.
- The safety hazard is great because the wiring harness is too much and too long, it will cause a series of safety hazards.
(2) Modular
It is very similar to the centralized BMS, but the modular BMS is divided into many identical sub-modules, and the wires of each package are connected to different parts inside the entire battery panel to monitor a certain area.
Although they are modules with the same function, there will actually be a module assigned as the main module to manage and dispatch the entire battery pack and communicate with the outside world. The other slave BMSs communicate with the master BMS through the communication bus, but their functions are the same.
Advantage:
- The centralized BMS is miniaturized and multiple cascaded, so it has most of the advantages of centralized, such as easy maintenance.
- The potential safety hazard is small. Due to the small scale of a single module, the wire from the sub-module to the single battery will be relatively short and can be closer to the battery, thus avoiding hidden dangers and errors caused by too-long wires.
- Easy to expand, more sub-modules can be added to achieve expansion.
Disadvantage:
- Additional wires need to be added. Compared with the centralized type, the modular stepper needs to be connected to the battery pack, and wire connections are also required between each module.
- The cost is high, the main reason that the functions of each module are the same, but not all functions will be used, which causes waste, especially the subordinate modules, which do not have many practical functions.
(3) Master-slave
An improved version of the module, which separates the modules according to the master-slave functions. Remove functions that are not used from the module, which can reduce a large cost.
The main BMS is responsible for relatively many functions, including calculation, forecasting, decision-making, communication, etc. The slave unit is basically only responsible for measurement.
Advantage:
- It is equivalent to inheriting most of the advantages of the modular structure while reducing the cost of expansion.
(4)Distributed
In the previous topologies, all kinds of electronic equipment will not be installed on a single battery, and are basically measured by throwing the wire.
But in the distributed system, our measurement unit and other electronic equipment are directly installed in the circuit board integrated with the single battery. The advantage of this is that compared with the previous ones, the connection between the BMS and the single battery basically wiped out.
Then it is a bit like the master-slave type in that it will also have a controller to be responsible for the calculation, prediction, decision-making, and other work. Communication between modules is based on the bus. In the car, we generally use the CAN bus.
Each of our units contains an acquisition circuit, and the MCU with CAN bus can send and receive information directly through bus communication.
Advantage:
- It has extremely high scalability and can be extended down to a single battery.
- The connection reliability is high, there are basically no excessively long cables, and the battery and the measurement circuit are closely integrated, which also reduces interference and errors. Security is also high.
- Easy to maintain, only a small unit needs to be replaced if something goes wrong.
Disadvantage:
- The cost is very high, because each unit adds a set of equipment, so the overall cost is very high.
- The volume is too large, and there is a measurement system next to each cell of each battery, which will affect the volume of the entire battery panel. Now some ICs can also be made very small, and this influencing factor will become weaker and weaker.
The Position of BMS in The Battery System
The master-slave integrated centralized BMS will be directly attached to the battery module (commonly found in less than 24 strings, 8 strings/10 strings/12 strings/16 strings/24 strings) in the PCBA state.
The master-slave separation distributed BMS will link the battery modules (less than 24 strings) with the slave control CSC, and then multiple slave control CSCs are cascaded to the BMU master control. The main control is responsible for communication and issuing instructions.
Summarize
The BMS battery management system is of great significance to protect the safety of energy storage battery packs, electric vehicles, charging station equipment and personnel. Whether BMS can be used normally in high and low-temperature extreme environments remains to be verified. Relevant R&D personnel should actively explore, continuously research new technologies, and promote BMS. The upgrade of the battery management system can better meet people's living needs.