Du début à la fin : le processus de fabrication des batteries au lithium
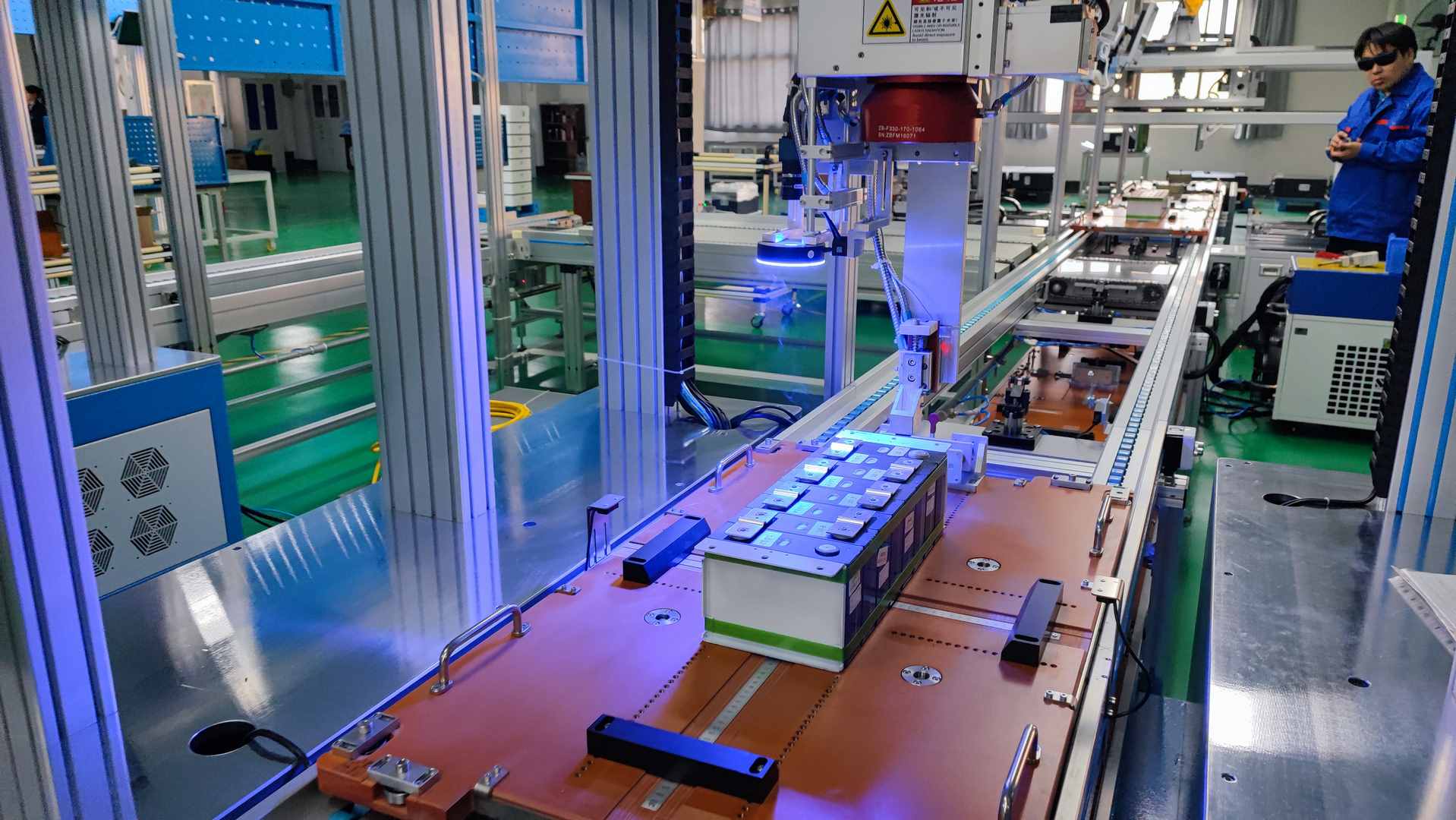
Les batteries au lithium sont largement utilisées dans diverses applications, notamment les appareils électroniques portables, les véhicules électriques et les systèmes de stockage d'énergie renouvelable. Pour répondre à la demande croissante de ces batteries, des processus de fabrication efficaces ont été développés pour garantir une production de haute qualité et rentable.
Vous êtes-vous déjà demandé comment les batteries au lithium, source d'énergie de nos smartphones, de nos véhicules électriques et même de certains systèmes d'énergie renouvelable, sont fabriquées du début à la fin ?
Dans cet article, nous vous ferons voyager à travers le processus complexe et complexe de batterie au lithium fabrication, mettant en avant chaque étape clé impliquée dans la création de ces dispositifs de stockage d'énergie puissants et portables.
Section 1 : Extraction et préparation des matières premières
L'acquisition de matières premières implique l'approvisionnement et l'obtention des matériaux nécessaires à la production de batteries, tels que le lithium, le cobalt et le nickel. Les sels de lithium, l'ingrédient clé, sont généralement extraits de gisements de saumure ou de minéraux de roche dure par une combinaison de procédés miniers et chimiques.
D'autre part, d'autres matériaux de batterie, comme la cathode, l'anode et l'électrolyte, proviennent de fournisseurs fiables, garantissant leur qualité et leur cohérence pour répondre aux exigences exigeantes de la production de batteries.
(1) Extraction de minerais riches en lithium
La première étape dans le batterie au lithium Le processus de fabrication consiste à extraire des minerais riches en lithium des sites miniers. Il s’agit d’une étape cruciale car elle fournit la matière première nécessaire à la production des batteries au lithium.
Voici trois aspects clés liés à l’extraction de minerais riches en lithium :
- Techniques minières : Il existe plusieurs techniques minières utilisées pour l’extraction de minerais riches en lithium. Une méthode courante est l'exploitation minière à ciel ouvert, où de grandes quantités de sol et de roche sont excavées pour atteindre les gisements de minerai. Une autre technique est l’exploitation minière souterraine, qui consiste à creuser un tunnel dans la terre pour accéder à des gisements plus profonds. Chaque méthode présente ses propres avantages et défis, en fonction de facteurs tels que les conditions géologiques et les considérations environnementales.
- Traitement du minerai : Une fois les minerais riches en lithium extraits, ils subissent un traitement supplémentaire pour extraire des minéraux précieux comme le carbonate de lithium ou l'hydroxyde de lithium. Les méthodes de traitement peuvent varier en fonction de facteurs tels que la qualité du minerai et les produits finaux souhaités. Les techniques courantes comprennent le concassage et le broyage du minerai en particules plus fines, suivis de traitements chimiques comme la flottation ou la lixiviation pour séparer et concentrer les minéraux souhaités.
- Impacts environnementaux : L'extraction de minerais riches en lithium peut avoir des impacts environnementaux importants si elle n'est pas correctement gérée. Les activités minières peuvent entraîner une dégradation des terres, une pollution de l'eau et des émissions de gaz à effet de serre. Pour atténuer ces impacts, diverses mesures doivent être mises en œuvre, telles que des plans de remise en état des zones minées, des systèmes de traitement de l'eau pour minimiser la pollution et l'adoption de pratiques durables tout au long du processus.
(2) Raffinage et purification du carbonate de lithium
Le raffinage et la purification du carbonate de lithium implique la mise en œuvre de diverses techniques pour assurer l'élimination des impuretés et la production de carbonate de lithium de haute qualité. Cette étape est cruciale dans le processus de production des batteries au lithium car elle affecte la qualité globale, le coût, l’efficacité et la conformité aux réglementations de fabrication.
La première étape consiste généralement à dissoudre le carbonate de lithium brut dans l’eau pour créer une solution. Cette solution est ensuite soumise à une filtration ou une centrifugation pour éliminer les impuretés insolubles telles que les particules solides.
Ensuite, divers traitements chimiques sont utilisés pour éliminer les autres impuretés présentes dans la solution. Ces traitements comprennent des réactions de précipitation utilisant des réactifs qui réagissent sélectivement avec des contaminants spécifiques, entraînant leur élimination de la solution.
Une fois ces impuretés éliminées, le liquide restant subit d’autres étapes de traitement comme l’évaporation ou la cristallisation pour concentrer et isoler le carbonate de lithium pur.
Le contrôle qualité joue un rôle essentiel tout au long de ce processus de raffinage et de purification. Le strict respect des réglementations de fabrication garantit que tous les niveaux d'impuretés se situent dans des limites acceptables pour les applications de batteries.
De plus, une surveillance continue grâce à des techniques analytiques telles que la spectroscopie ou la chromatographie permet aux fabricants d'identifier tout écart potentiel par rapport aux normes de pureté souhaitées dès le début de la production.
(3) Préparation des matériaux cathodiques
La préparation des matériaux cathodiques implique une série d'étapes méticuleuses pour assurer la production de composants hautes performances qui contribuent à l'avancement et au succès de batterie au lithium technologie.
La première étape de ce processus consiste à sélectionner et à préparer le matériau actif, généralement un oxyde métallique tel que l'oxyde de lithium-cobalt (LiCoO2), l'oxyde de lithium-manganèse (LiMn2O4) ou le phosphate de fer et de lithium (LiFePO4).
Le matériau actif est ensuite mélangé à des additifs conducteurs tels que du noir de carbone ou du graphite pour améliorer le transfert d'électrons au sein de la cathode.
Ce mélange est soigneusement mélangé pour obtenir une distribution homogène, garantissant des performances uniformes sur toute l'électrode.
Une fois le matériau actif et les additifs conducteurs combinés, ils sont déposés sur un collecteur de courant, généralement constitué d’une feuille d’aluminium.
Ce processus de revêtement nécessite de la précision pour obtenir une épaisseur et une uniformité optimales.
Après le revêtement, la cathode subit un processus de séchage pour éliminer tous les solvants utilisés lors du mélange et du revêtement. Cela garantit que le produit final présente une excellente stabilité et conductivité électrique.
(4) Production de matériaux d'anode
Une étape essentielle dans la fabrication des batteries lithium-ion implique la production des matériaux d’anode. L'anode est l'une des deux électrodes d'une batterie et joue un rôle crucial dans les performances et l'efficacité globales de la batterie.
Généralement, le graphite est utilisé comme matériau principal pour les anodes en raison de son excellente conductivité et stabilité.
Le processus de production commence par la sélection de poudre de graphite de haute qualité, qui est ensuite mélangée à des liants et des solvants pour former une suspension. Cette suspension est ensuite appliquée sur un substrat en feuille de cuivre à l'aide d'une technique appelée revêtement à la racle ou revêtement rouleau à rouleau. Après revêtement, il subit des processus de séchage et de calandrage pour garantir l’uniformité et améliorer l’adhérence.
Une fois l’électrode de graphite préparée, elle passe par plusieurs étapes supplémentaires pour améliorer ses propriétés électrochimiques.
L’une de ces étapes consiste à appliquer une fine couche de matériau protecteur, tel que des nanotubes de carbone ou de l’oxyde de silicium, sur la surface du graphite. Cette couche protectrice aide à prévenir la dégradation pendant les cycles de charge et de décharge en réduisant les réactions secondaires entre les ions lithium et les électrolytes.
De plus, divers additifs peuvent être incorporés au matériau de l'anode pour améliorer encore ses performances, tels que des agents conducteurs comme le noir de carbone ou des nanoparticules métalliques.
Dans l’ensemble, la production de matériaux d’anode de haute qualité nécessite un contrôle précis de divers paramètres, notamment la distribution granulométrique, la teneur en liant, l’épaisseur du revêtement et la composition des additifs. Ces facteurs ont un impact direct sur la capacité, la stabilité du cycle, la capacité de débit et la sécurité des batteries lithium-ion.
(5) Fabrication de séparateurs
La fabrication des séparateurs est une étape critique dans la production de batteries lithium-ion, car elle implique la fabrication d'un matériau fin et poreux qui agit comme une barrière physique entre l'anode et la cathode, permettant le mouvement sélectif des particules. Ions lithium tout en évitant les courts-circuits et en améliorant la batterie sécurité.
Le processus commence par la sélection de matières premières appropriées telles que le polyéthylène ou le polypropylène, couramment utilisés en raison de leur point de fusion élevé et de leur stabilité chimique. Ces matériaux sont ensuite fondus et extrudés sous forme de film à l’aide d’un équipement spécialisé.
Pour garantir des performances optimales, le film séparateur subit plusieurs traitements supplémentaires. Tout d’abord, il est soumis à un étirement dans le sens machine et dans le sens transversal pour améliorer sa résistance mécanique et sa porosité. Ce processus d'étirement aligne les chaînes polymères au sein du film, créant des canaux microscopiques qui facilitent le transport des ions tout en maintenant l'intégrité structurelle.
Ensuite, le séparateur est recouvert d'une couche de céramique pour améliorer encore sa stabilité thermique et éviter les courts-circuits internes provoqués par le contact avec les particules métalliques des électrodes.
En suivant ces étapes de fabrication précises, les fabricants peuvent produire des séparateurs répondant à des normes de qualité strictes tout en garantissant un transport efficace des ions au sein des batteries lithium-ion.
Section 2 : Préparation et revêtement des électrodes
Cette discussion se concentre sur le processus de préparation et de revêtement des électrodes dans la fabrication des batteries au lithium. Il englobe divers points clés tels que le mélange et le mélange des matières actives, les techniques de préparation et de revêtement des boues, les processus de séchage et de calandrage et les mesures de contrôle qualité.
(1) Mélange et mélange de matériaux actifs
Au cours de l’étape de mélange et de mélange du processus de fabrication des batteries au lithium, divers matériaux actifs sont soigneusement combinés dans un environnement contrôlé pour créer un mélange homogène.
Cette étape est cruciale car elle garantit que les matériaux actifs, tels que l'oxyde de lithium et de cobalt pour la cathode et le graphite ou le silicium pour l'anode, sont répartis uniformément dans toute la batterie. Atteindre une distribution uniforme est essentiel pour des performances et une efficacité optimales de la batterie.
Pour ce faire, les fabricants utilisent des équipements spécialisés tels que des mélangeurs ou des mélangeurs capables de traiter de grands volumes de matériaux. Ces machines offrent un contrôle précis de facteurs tels que la vitesse de rotation, le temps de mélange et la température pour obtenir des résultats cohérents. Les matériaux actifs sont généralement mélangés avec des liants et des solvants pour former une consistance semblable à une suspension qui peut être facilement appliquée sur les collecteurs de courant pendant le revêtement des électrodes. Le maintien d'un environnement contrôlé exempt de contaminants est crucial pendant cette étape pour éviter que des impuretés n'affectent la qualité de la batterie.
Voici un tableau intéressant présentant trois matériaux actifs clés utilisés dans les batteries lithium-ion :
Matériau actif | Rôle dans la batterie | Avantages |
---|---|---|
Oxyde de lithium-cobalt (LiCoO2) | Matériau cathodique | Haute densité énergétique, bonne stabilité cyclable |
Graphite | Matériau de l'anode | Excellente conductivité, faible coût |
Silicium | Matériau de l'anode | Haute capacité, potentiel pour une densité énergétique plus élevée |
Ce tableau montre comment chaque matériau actif apporte des caractéristiques uniques pour améliorer les performances de la batterie. En comprenant mieux ces composants, les individus peuvent mieux comprendre comment les progrès dans la technologie des batteries au lithium peut conduire vers un avenir où nous jouirons d’une plus grande liberté grâce à des appareils électroniques portables dotés de sources d’énergie plus durables.
(2) Techniques de préparation et de revêtement des boues
Le tri et le classement des cellules constituent une étape critique du processus de fabrication des batteries au lithium, garantissant que seules les cellules répondant aux spécifications requises sont utilisées pour la production ultérieure.
La préparation du lisier consiste à créer un mélange de matières actives, de liants, de solvants et d'additifs pour former une substance pâteuse homogène appelée bouillie. Cette suspension agit comme un élément crucial dans la production d'électrodes pour batteries à lithium.
Pour fournir une compréhension complète des techniques de préparation des boues et de revêtement, examinons quatre aspects clés :
- Formulation de boue : La première étape de la préparation d'une boue consiste à sélectionner soigneusement les matériaux actifs appropriés en fonction de leurs propriétés électrochimiques et des caractéristiques de performance souhaitées. Des liants sont ensuite ajoutés pour améliorer la cohésion au sein de la structure de l’électrode. Le choix des solvants dépend de facteurs tels que le contrôle de la viscosité et les caractéristiques de séchage. Enfin, des additifs sont incorporés pour améliorer l’adhésion entre les couches ou améliorer les performances de la batterie.
- Méthodes de mélange : Il est primordial d’obtenir une dispersion uniforme des matières actives dans la boue pour obtenir des performances constantes de la batterie. Les méthodes traditionnelles impliquent une agitation mécanique ou un broyage à boulets pour garantir un mélange complet sans endommager l'intégrité des particules. Des techniques plus avancées comme la sonication ou le mélange à fort cisaillement ont également été introduites pour obtenir une meilleure dispersion des nanomatériaux.
- Revêtement en boue : Une fois correctement mélangée, la boue est appliquée sur les substrats des collecteurs de courant par diverses techniques de revêtement telles que le revêtement à la racle ou les méthodes d'extrusion à filière à fente. Ces procédés permettent des épaisseurs de dépôt contrôlées tout en assurant une répartition uniforme sur de grandes surfaces.
- Séchage et solidification : Après application, l'évaporation du solvant doit se produire efficacement sans provoquer de fissures ou de défauts dans la structure du film d'électrode. Des conditions de séchage contrôlées à l'aide de fours ou de systèmes continus rouleau à rouleau permettent l'élimination progressive des solvants tout en préservant l'intégrité structurelle.
(3) Processus de séchage et de calandrage
Le processus de séchage et de calandrage est essentiel pour obtenir des électrodes de haute qualité présentant une intégrité structurelle et des performances optimales dans les batteries au lithium. En contrôlant soigneusement ces étapes, les fabricants peuvent produire des électrodes présentant une uniformité et une cohérence dans toute leur structure.
Après l’étape de revêtement en suspension, le solvant présent dans l’électrode doit être éliminé par un processus de séchage. Ceci est généralement réalisé en soumettant les électrodes enrobées à des températures élevées, provoquant l'évaporation du solvant. Des précautions doivent être prises lors de cette étape pour assurer un séchage uniforme dans toute l'électrode, car un séchage inégal peut entraîner des défauts tels que des fissures ou un délaminage.
Une fois séchées, les électrodes subissent un calandrage qui consiste à les comprimer sous haute pression pour améliorer leurs propriétés mécaniques. Cette étape permet d'augmenter la densité et l'épaisseur de l'électrode tout en améliorant sa conductivité électrique.
Le calandrage permet également d’éliminer les solvants restants qui pourraient ne pas s’être complètement évaporés pendant le séchage. La pression appliquée lors du calandrage assure un bon contact entre les matériaux actifs et les collecteurs de courant, optimisant ainsi le transfert d'électrons au sein du système de batterie.
Section 3 : Assemblage et formation des cellules
Au cours du processus de chaîne d’assemblage des batteries au lithium, divers composants sont soigneusement intégrés pour créer une cellule fonctionnelle. La chaîne d'assemblage de cellules est conçue pour rationaliser le processus de production et garantir la cohérence du produit final. Il se compose généralement de plusieurs stations où différentes tâches sont exécutées séquentiellement.
(1) Empilage et enroulement d'électrodes
L'empilement et le bobinage des électrodes sont une étape critique dans le processus de chaîne d'assemblage des batteries au lithium. Ce processus est essentiel pour optimiser les performances et l'efficacité des batteries au lithium.
Le processus d'empilement et d'enroulement d'électrodes implique généralement plusieurs couches d'électrodes positives et négatives alternées, séparées par de fines couches de matériau séparateur. Les électrodes sont constituées de matériaux actifs, tels que l'oxyde de lithium-cobalt ou le graphite, qui stockent et libèrent de l'énergie électrique pendant le fonctionnement de la batterie.
Tableau : Techniques d'empilement d'électrodes
Technique | Description |
---|---|
Rouleau de gelée | Enroulement continu d'électrodes et de matériau séparateur autour d'un noyau central pour créer une structure en spirale |
Pliage/Plissage | Pliage ou plissage des électrodes pour augmenter leur surface avant de les empiler |
Zigzag | Disposition en zigzag alternée des électrodes positives et négatives pour améliorer la capacité globale de la batterie |
Empilement croisé | Disposition transversale de plusieurs piles d'électrodes pour augmenter la densité énergétique |
Co-extrusion | Extrusion simultanée de différents matériaux d'électrode dans une bande continue |
(2) Placement du séparateur
Le placement du séparateur est une étape cruciale dans le processus de la chaîne d'assemblage des batteries au lithium, car il implique le positionnement du matériau séparateur entre les électrodes positives et négatives pour permettre un transport efficace des ions pendant le fonctionnement de la batterie.
Le séparateur joue un rôle essentiel en empêchant tout contact direct entre les électrodes, ce qui pourrait entraîner des courts-circuits ou d'autres risques pour la sécurité. Il agit comme une barrière physique qui permet uniquement la circulation des ions tout en bloquant le mouvement des électrons. Cela garantit que la batterie fonctionne correctement et efficacement.
Voici quatre aspects importants liés au placement du séparateur :
- Sélection du matériau : Le choix du matériau du séparateur est essentiel car il détermine ses caractéristiques de performance. Généralement, les séparateurs sont fabriqués à partir de matériaux polymères tels que le polyéthylène (PE) ou le polypropylène (PP). Ces matériaux offrent une stabilité thermique élevée, une bonne résistance mécanique et une excellente mouillabilité des électrolytes.
- Contrôle de l'épaisseur : L'épaisseur du séparateur joue un rôle important dans la détermination de sa conductivité ionique et des performances globales de la batterie. Un contrôle précis de l’épaisseur du séparateur est essentiel pour obtenir un transport optimal des ions et éviter une résistance excessive au sein de la batterie.
- Uniformité et alignement : lors du placement du séparateur, il est essentiel de garantir l'uniformité et l'alignement approprié pour garantir des performances constantes de la batterie sur toutes les cellules. Toute variation ou désalignement peut entraîner des points chauds localisés ou une répartition inégale des ions dans la batterie, affectant son efficacité globale.
- Propriétés adhésives : Pour maintenir le tout en toute sécurité, une couche adhésive peut être appliquée lors de la mise en place du séparateur. Cet adhésif doit avoir une bonne adhérence aux deux électrodes tout en conservant sa flexibilité pour s'adapter aux changements de volume pendant les cycles de charge-décharge sans compromettre l'intégrité des cellules.
(3) Introduction de l'électrolyte
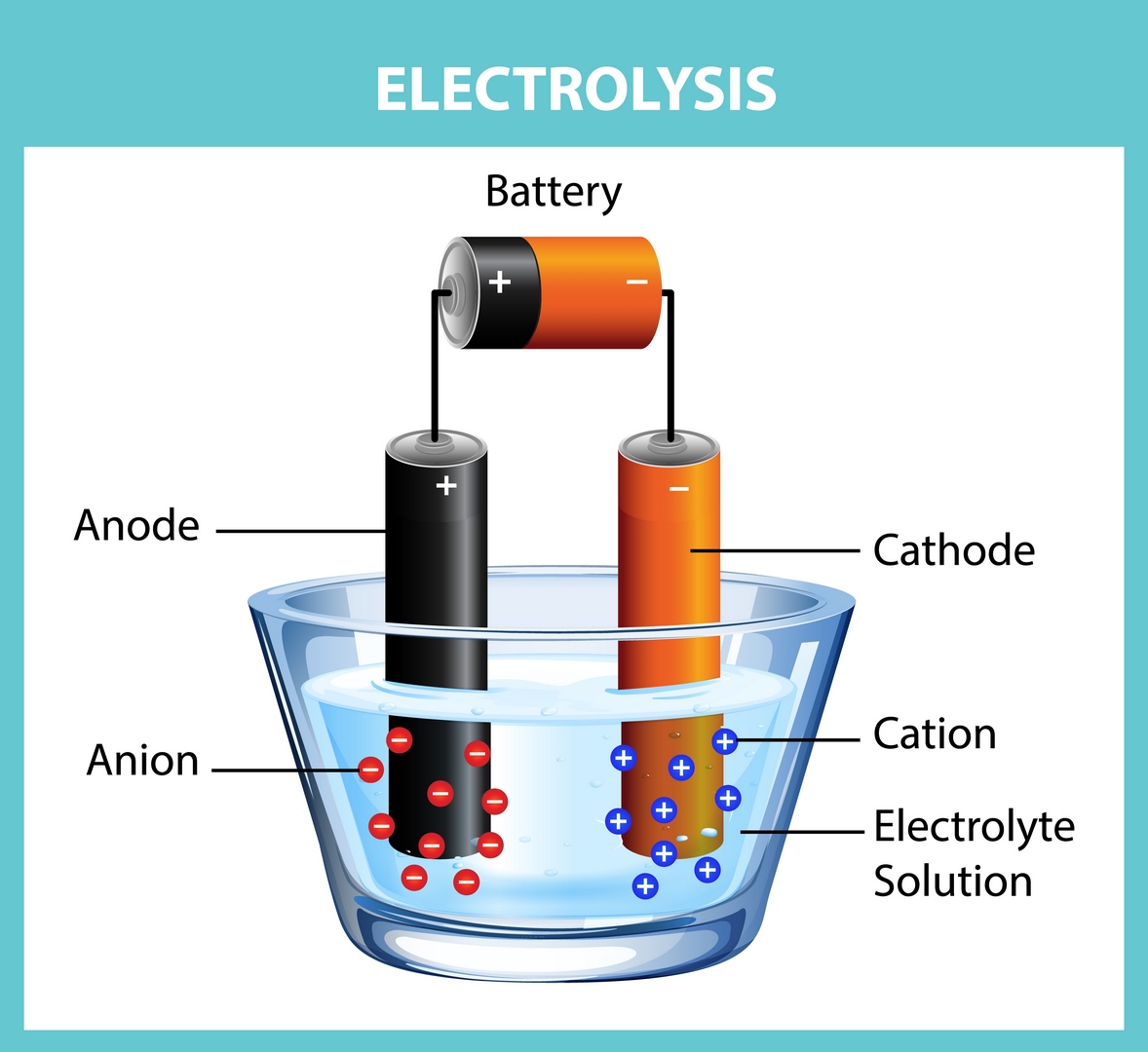
L'introduction d'électrolytes est un élément crucial étape du processus de chaîne d’assemblage des batteries au lithium, car il s'agit d'incorporer une solution conductrice qui permet le transport des ions au sein de la batterie pour un fonctionnement efficace.
Les électrolytes jouent un rôle essentiel en facilitant le mouvement des ions entre les électrodes positives et négatives, permettant ainsi la circulation du courant électrique. Généralement, les batteries lithium-ion utilisent des électrolytes liquides constitués de sels de lithium dissous dans des solvants organiques. Ces solvants offrent une conductivité élevée et sont capables de dissoudre efficacement les sels de lithium.
Lors de l'introduction des électrolytes, la précision et l'exactitude sont primordiales pour garantir des performances optimales de la batterie. L'électrolyte doit être soigneusement injecté dans chaque cellule ou pochette pour obtenir une répartition uniforme dans toute la batterie.
Ce processus nécessite un équipement et des systèmes de contrôle sophistiqués pour maintenir un volume constant et empêcher tout fuites ou des bulles d'air qui pourraient compromettre l'intégrité de la batterie. De plus, les fabricants doivent respecter des mesures de sécurité strictes lors de la manipulation des électrolytes, car ils peuvent être inflammables et dangereux en cas de mauvaise manipulation.
(4) Scellement et encapsulation
Le scellement et l’encapsulation sont des étapes critiques dans le processus de la chaîne d’assemblage des batteries au lithium, garantissant la protection et l’intégrité des composants de la batterie. Ce processus consiste à enfermer les cellules de la batterie dans une barrière protectrice pour empêcher les contaminants externes de pénétrer et de causer des dommages ou une dégradation aux composants internes. Cela aide également à maintenir la stabilité de la solution électrolytique à l’intérieur de la batterie.
Lors du scellement et de l’encapsulation, plusieurs étapes importantes sont prises pour garantir une étanchéité sûre et fiable :
- Soudage : La première étape consiste à souder ou à fusionner divers composants du boîtier de la batterie, tels que des boîtes ou des bouchons métalliques. Cela crée un joint hermétique qui empêche toute fuite d’électrolytes ou de gaz depuis l’intérieur de la cellule.
- Isolation : Après le soudage, des matériaux isolants sont appliqués autour des zones soudées pour fournir une protection supplémentaire contre les dommages physiques, les vibrations et les courts-circuits électriques. Ces matériaux isolants peuvent inclure des films ou des tampons polymères qui aident à isoler différentes parties de la batterie.
- Revêtement : Enfin, un revêtement protecteur est appliqué sur l'ensemble du boîtier pour améliorer encore sa résistance à l'humidité, à la corrosion et à d'autres facteurs environnementaux. Ce revêtement peut être constitué de divers matériaux comme des résines époxy ou des polymères spécialisés qui constituent une barrière imperméable.
En suivant ce processus méticuleux de scellement et d'encapsulation, le batterie au lithium supérieure les fabricants s'assurent que leurs produits répondent à des normes de qualité strictes tout en offrant des performances optimales tout au long de leur durée de vie. Cette attention aux détails garantit que les utilisateurs ont accès à des batteries de haute qualité qui offrent une fiabilité tout en répondant aux exigences de sécurité dans diverses applications allant de l'électronique grand public aux véhicules électriques.
(5) Cyclisme en formation
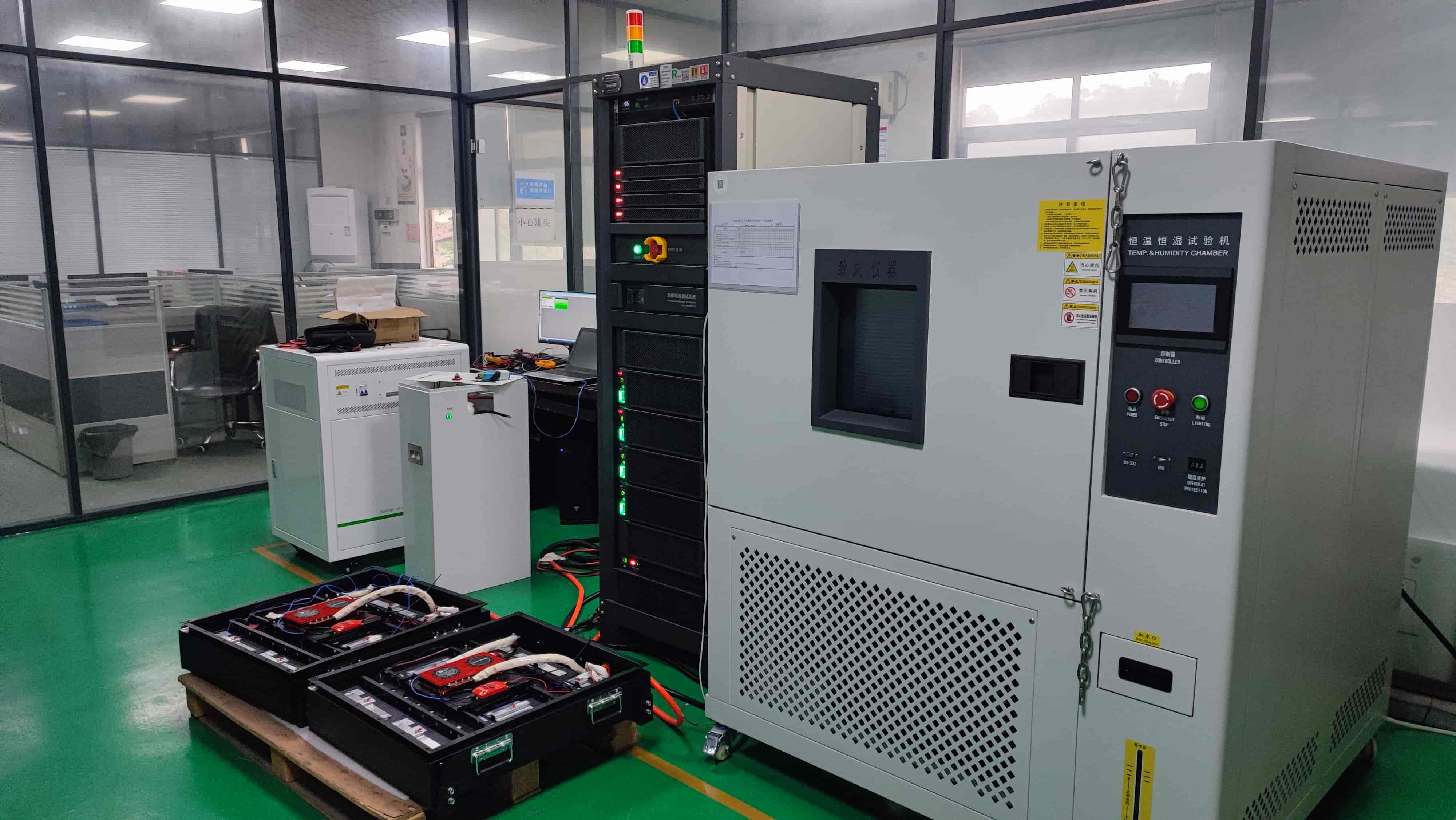
Le cycle de formation est une étape cruciale dans le processus de la chaîne d'assemblage des batteries au lithium, garantissant des performances et une capacité optimales en soumettant les cellules à une série de cycles de charge et de décharge avant qu'elles ne soient prêtes à l'emploi.
Ce processus consiste à charger la batterie à sa capacité maximale, puis à la décharger complètement. Ceux-ci facturent et les cycles de décharge aident à activer les différents composants de la batterie, tels que les matériaux de cathode et d'anode, l'électrolyte et le séparateur.
Pendant le cycle de formation, toutes impuretés ou défauts présents dans la batterie sont identifiés et traités. Cela contribue à améliorer l’efficacité globale de la batterie en éliminant les points faibles potentiels ou les zones de performances réduites.
De plus, le cycle de formation aide également à stabiliser la tension de sortie de la batterie au fil du temps, garantissant ainsi une fourniture d'énergie constante tout au long de sa durée de vie.
L'objectif du cycle de formation est d'optimiser à la fois la densité énergétique et durée de vie des batteries au lithium. En les soumettant à ce processus de tests rigoureux dès le début de leur production, les fabricants peuvent identifier tout problème ou faiblesse potentiel avant qu'ils n'atteignent les consommateurs.
Cela améliore non seulement les performances, mais renforce également la sécurité en minimisant le risque de dysfonctionnements ou de pannes pendant l'utilisation.
Section 4 : Tests et assurance qualité
(1) Évaluation des performances
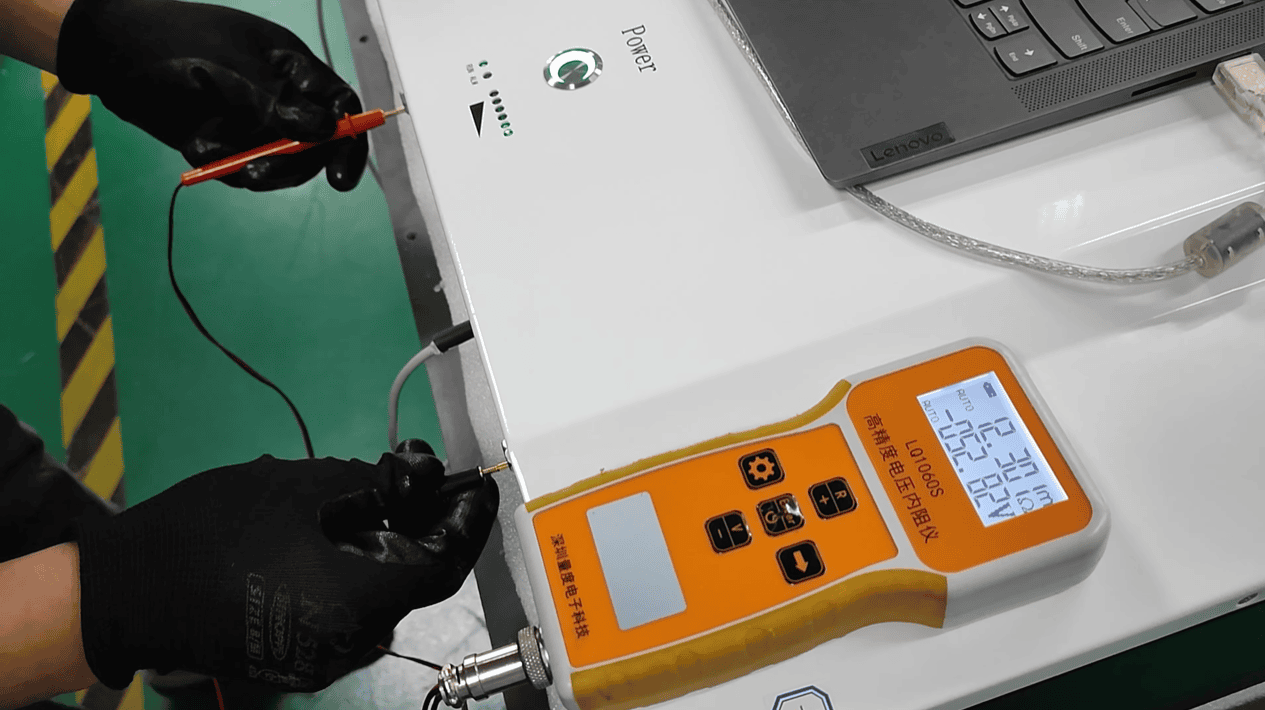
L'évaluation des performances lors de la fabrication des batteries au lithium garantit que chaque unité répond à des normes de qualité strictes en matière de capacité, de stabilité de tension et de durée de vie.
Un test clé est la mesure de tension (OCV), qui indique la différence de potentiel entre les bornes positives et négatives lorsqu'aucun courant ne circule. OCV fournit des informations cruciales sur l’état de charge et santé de la batterie cellule.
Un autre aspect clé évalué lors de ce test est capacité, qui fait référence à la quantité de charge qu’une batterie peut stocker. Les tests de capacité aident fabricants comprendre combien d'énergie peut être stockée et fournie par la batterie dans différentes conditions.
Le test de résistance interne de la batterie est également important. En mesurant cette résistance, il est possible d’évaluer l’efficacité avec laquelle l’énergie peut être transférée au sein de la cellule de la batterie.
De plus, des tests de durée de vie sont effectués pour déterminer combien de cycles de charge-décharge une batterie au lithium peut supporter avant que sa capacité ne se dégrade de manière significative.
Enfin, des tests de sécurité tels que l'analyse de stabilité thermique sont effectués pour garantir que les cellules de la batterie ne présentent aucun risque de surchauffe ou d'incendie.
Grâce à ces évaluations rigoureuses, le principaux fabricants de batteries au lithium s'efforcer de produire des batteries de haute qualité qui répondent à la fois aux exigences de performance et aux attentes des consommateurs tout en garantissant la sécurité tout au long de leur cycle de vie.
(2) Tests de sécurité
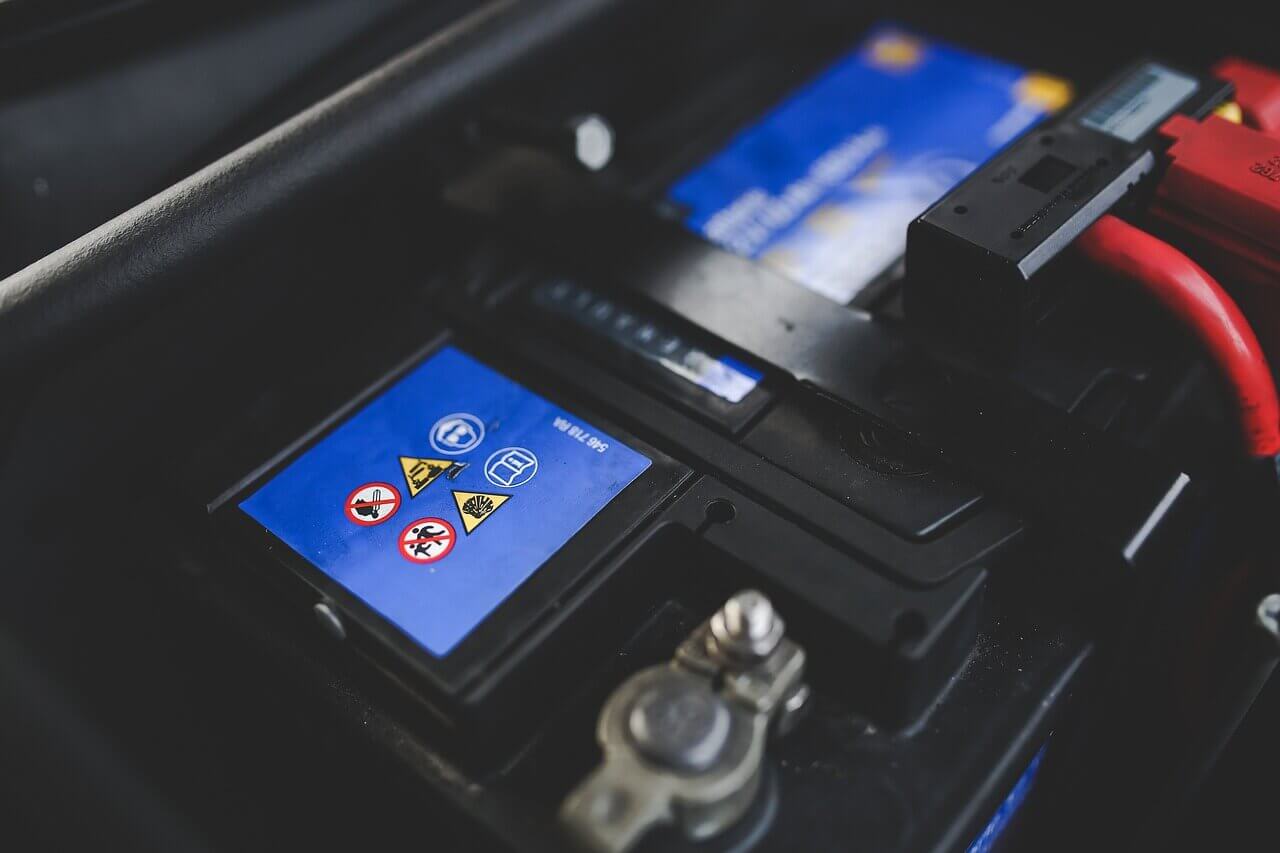
Les tests de sécurité font partie intégrante du flux de fabrication des batteries au lithium, car ils garantissent que les risques potentiels associés à la température, à la surcharge et aux courts-circuits sont identifiés et atténués.
Température les tests consistent à soumettre les batteries à des conditions extrêmes pour évaluer leurs performances et leur stabilité. Cela implique de les exposer à des températures élevées et basses pour évaluer leur capacité à fonctionner en toute sécurité dans divers environnements.
Surcharge des tests sont effectués pour déterminer la réponse de la batterie lorsqu'elle est soumise à des courants de charge excessifs ou à des périodes de charge prolongées. En évaluant le comportement de la batterie dans ces conditions, les fabricants peuvent identifier tout risque potentiel pour la sécurité, tel qu'un emballement thermique ou une décomposition de l'électrolyte.
Les tests de court-circuit constituent un autre aspect crucial de l’évaluation de la sécurité dans la fabrication des batteries au lithium. Il s’agit de créer intentionnellement une connexion directe entre les bornes positives et négatives d’une cellule de batterie à l’aide d’un matériau conducteur.
Ce test permet d'évaluer la capacité de la batterie à résister aux courts-circuits internes ou externes sans subir de panne catastrophique ou d'emballement thermique. Les fabricants analysent des paramètres tels que le flux de courant, la chute de tension et les changements de température au cours de ce processus.
(3) Mesures de contrôle de la qualité
Dans le sous-thème précédent, nous avons exploré les procédures de tests de sécurité menées au cours de la fabrication de batteries au lithium processus. Ces tests comprennent l'évaluation des performances en température, la protection contre les surcharges et la prévention des courts-circuits pour garantir le fonctionnement sûr de ces batteries.
Examinons maintenant un autre aspect crucial de ce processus : les mesures de contrôle qualité.
Le contrôle qualité est un aspect fondamental de la fabrication des batteries au lithium qui garantit des performances et une fiabilité constantes. En mettant en œuvre des mesures de contrôle qualité rigoureuses à chaque étape de la production, les fabricants peuvent identifier et corriger tout défaut ou incohérence de leurs produits. Plusieurs mesures clés de contrôle de la qualité sont utilisées, notamment :
- Inspection visuelle : cela implique d'examiner soigneusement chaque batterie pour détecter tout défaut physique tel que des bosses, des fuites ou des connexions incorrectes. Les fabricants utilisent des techniques d'imagerie avancées et des systèmes automatisés pour détecter même les imperfections mineures susceptibles d'affecter les performances de la batterie.
- Tests électrochimiques : Pour évaluer avec précision les caractéristiques électriques des batteries, divers tests électrochimiques sont effectués. Ces tests évaluent des paramètres tels que la capacité, la résistance interne, les profils de tension dans des conditions de charge et la durée de vie pour garantir des capacités de stockage d'énergie optimales.
- Analyse des matériaux : le contrôle qualité comprend également l'analyse de la composition et de la pureté des matériaux utilisés dans les composants de la batterie tels que les électrodes et les électrolytes. Cette analyse permet d'identifier les impuretés ou variations susceptibles d'avoir un impact sur les performances ou la sécurité de la batterie.
Section 5 : Assemblage du bloc-batterie
Ce paragraphe abordera les points clés liés à la batterie assemblage du pack dans le lithium processus de fabrication des batteries.
(1) Intégration de cellules dans des packs
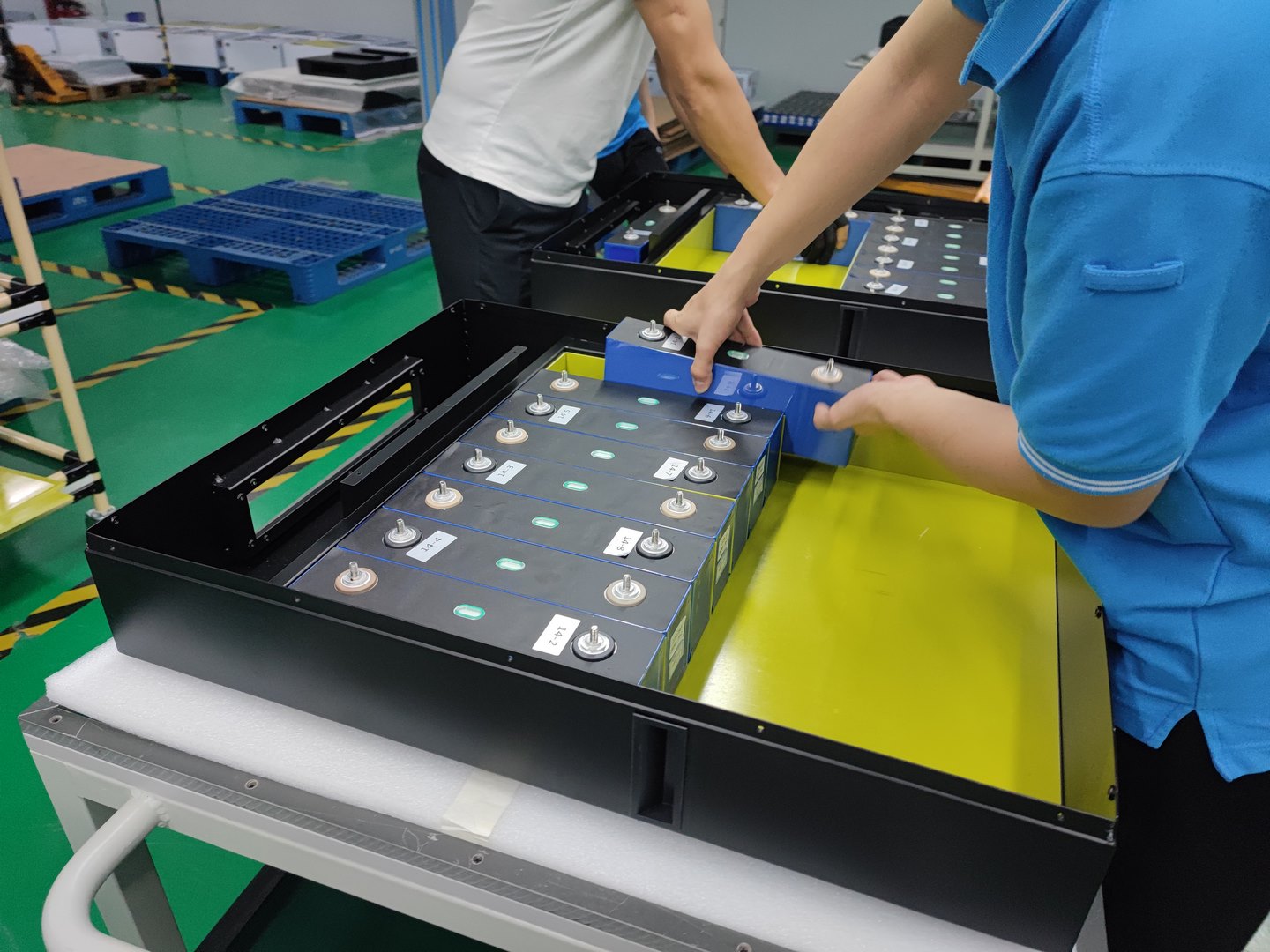
Le processus d'intégration de cellules de batterie individuelles dans des packs nécessite un examen attentif de facteurs tels que la conception des modules, les connexions électriques et les mécanismes de sécurité.
La conception des modules joue un rôle crucial pour garantir l’intégration efficace et efficiente des cellules de batterie. Les modules sont conçus pour accueillir un nombre spécifique de cellules et fournir un support structurel tout en permettant également un refroidissement et une gestion thermique appropriés. De plus, la conception doit prendre en compte des facteurs tels que la répartition du poids, l'utilisation de l'espace et la facilité d'assemblage.
Les connexions électriques entre les cellules de la batterie au sein d’un pack sont essentielles pour obtenir des performances optimales. Ces connexions doivent être soigneusement conçues pour minimiser la résistance et assurer une répartition uniforme du courant entre les cellules. Diverses techniques telles que le soudage par points ou le soudage par ultrasons peuvent être utilisées pour établir des connexions électriques fiables entre les bornes des cellules.
(2) Systèmes de gestion thermique
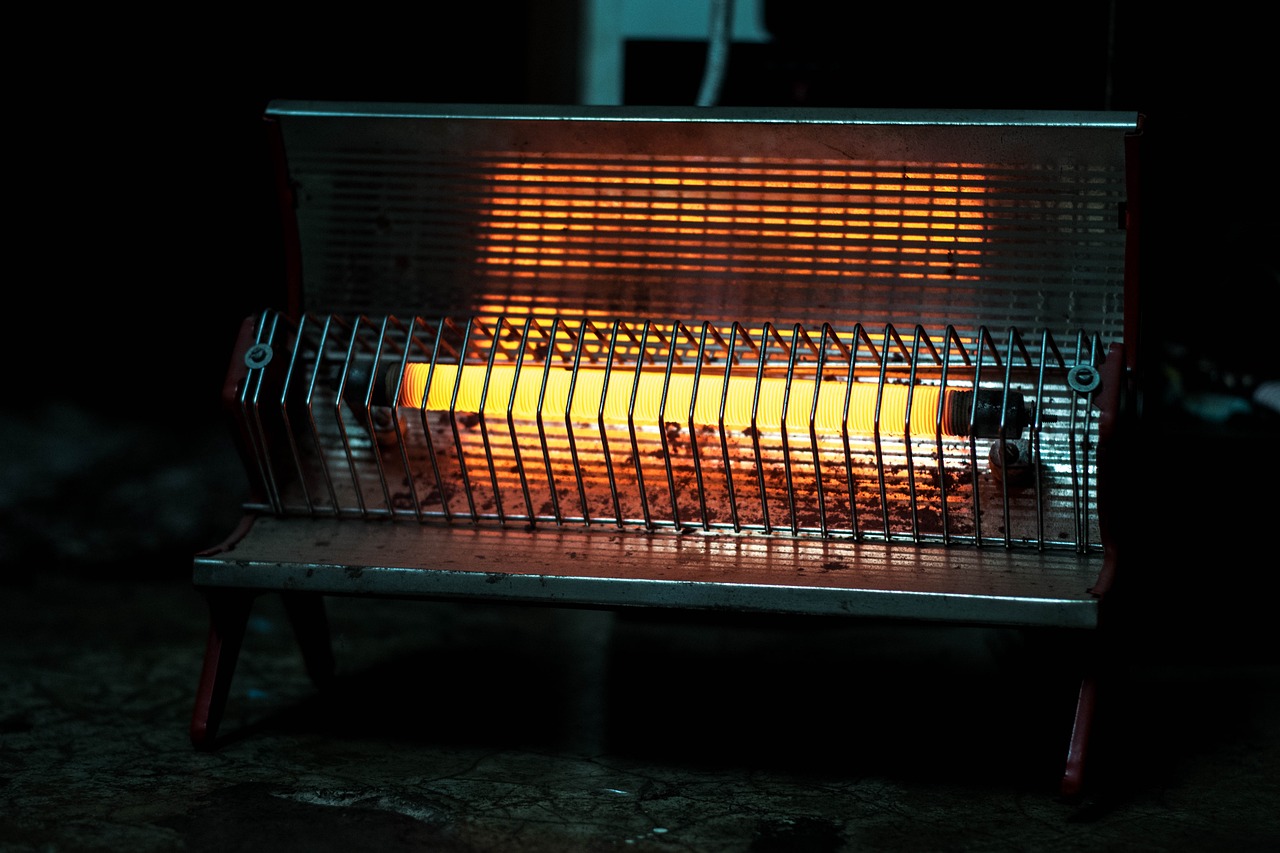
Systèmes de gestion thermique jouent un rôle crucial pour garantir le fonctionnement efficace et la longévité des batteries intégrées, car elles aident à réguler les niveaux de température et à prévenir un échauffement excessif qui pourrait entraîner une dégradation des performances ou des risques pour la sécurité.
Ces systèmes sont conçus pour dissiper la chaleur générée pendant les processus de charge et de décharge de la batterie, maintenant les cellules dans des plages de température optimales.
Une approche courante consiste à utiliser des méthodes de refroidissement passives, telles que des dissipateurs thermiques ou des matériaux thermiquement conducteurs, qui transfèrent la chaleur des cellules vers l'environnement. De plus, des techniques de refroidissement actif peuvent être utilisées, telles que des systèmes de refroidissement par liquide ou par air, qui éliminent activement la chaleur du bloc-batterie par circulation.
Pour parvenir à une gestion thermique efficace, divers facteurs doivent être pris en compte. La conception du pack doit inclure un espacement approprié entre les cellules pour permettre une circulation efficace de l'air ou du liquide de refroidissement. De plus, des matériaux isolants peuvent être appliqués pour minimiser le transfert de chaleur entre des cellules adjacentes ou des environnements externes.
De plus, les systèmes avancés de gestion thermique intègrent des capteurs et des algorithmes de contrôle qui surveillent les variations de température en temps réel et ajustent les mécanismes de refroidissement en conséquence. Ces systèmes intelligents permettent une régulation précise des niveaux de température dans des limites étroites, optimisant ainsi les performances de la batterie tout en garantissant la sécurité.
(3) Systèmes de gestion de batterie
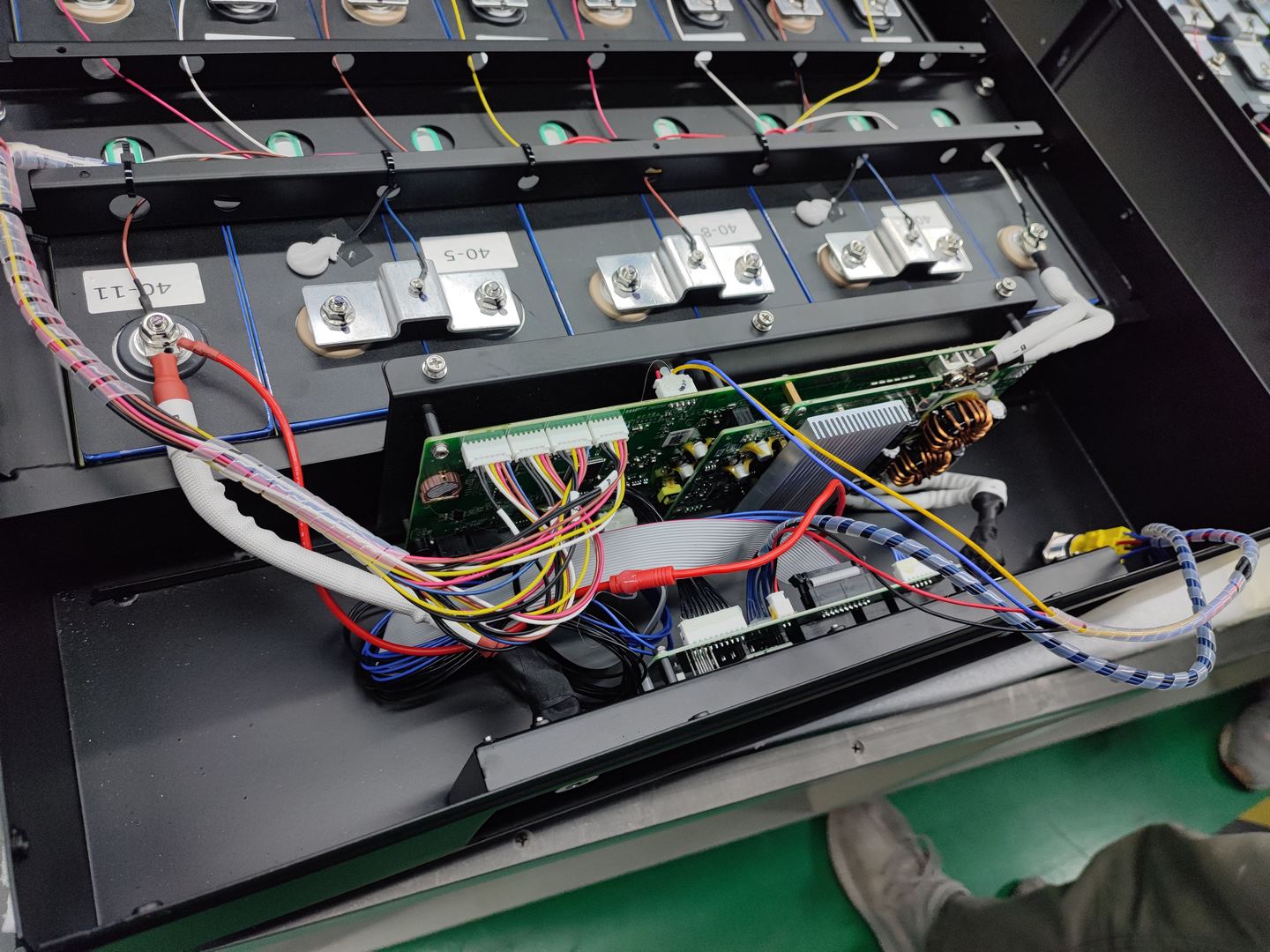
Systèmes de gestion de batterie (BMS) jouent un rôle central en garantissant le fonctionnement efficace et sûr des batteries intégrées en surveillant les paramètres cruciaux et en contrôlant diverses fonctions pour optimiser les performances et la longévité.
Un BMS est chargé de surveiller l’état de charge, l’état de santé et l’état de fonctionnement de chaque cellule individuelle d’une batterie. Il mesure en permanence la tension, le courant, la température et d'autres paramètres pertinents pour garantir que chaque cellule fonctionne dans ses limites de sécurité.
En surveillant en permanence ces paramètres, le BMS peut détecter toute anomalie ou écart par rapport à un fonctionnement optimal et prendre des mesures correctives pour atténuer les risques potentiels.
En plus de surveiller les cellules, un BMS gère également diverses fonctions pour optimiser les performances et la longévité. Il contrôle les processus de charge en régulant le flux de courant dans la batterie, empêchant ainsi la surcharge ou la sous-charge pouvant entraîner une dégradation ou une réduction de la capacité.
Le BMS équilibre également les niveaux de charge entre les cellules individuelles pour éviter que certaines cellules ne soient surchargées tandis que d'autres restent sous-chargées. Cet équilibre garantit une usure uniforme sur toutes les cellules et maximise l’utilisation globale de la capacité.
De plus, le BMS offre une protection contre les surintensités, les courts-circuits, la surchauffe et d'autres événements potentiellement dangereux qui pourraient compromettre la sécurité ou endommager la batterie.
Principaux fabricants sud-africains de batteries au lithium
Alimentez votre vie en toute confiance en utilisant RÉCOLTE Batterie Lifepo4. Nos batteries offrent des avantages inégalés qui redéfiniront votre expérience énergétique. Voici pourquoi:
- Garantie imbattable : Ayez l'esprit tranquille grâce à notre solution leader du secteur Garantie 12 ans. Nous garantissons la qualité et la longévité de nos batteries.
- Qualité supérieure: Fabriqué avec CATL marque Batteries, reconnues comme les meilleures au monde, nos produits offrent des performances et une durabilité inégalées.
- Cycles d'alimentation sans fin : Découvrez la liberté jusqu'à 8 000 cycles, garantissant que votre batterie dure plus longtemps et fournit une puissance constante pour les années à venir.
- Compatibilité transparente : Notre batterie Lifepo4 s'intègre sans effort à plus de 30 onduleur marques, offrant polyvalence et compatibilité pour vos besoins spécifiques.
- Technologie de pointe: Alimentées par notre ligne de production automatique intelligente et notre technologie de soudage laser de précision, nos batteries sont construites avec la plus grande précision et fiabilité.
- Service client: 7 jours à 24 heures, fournissant un professionnel entretien et utilisation de la batterie au lithium compétences
Choisissez HARVEYPOW pour des batteries qui redéfinissent l'excellence. Ne vous contentez pas de moins lorsque vous pouvez dynamiser votre vie avec le meilleur. Embrassez l'avenir de l'énergie avec la batterie HARVEYPOW Lifepo4 dès aujourd'hui !
Section 6 : Progrès dans les technologies de fabrication de batteries
Cette discussion se concentrera sur les progrès des technologies de fabrication de batteries, en particulier les batteries à semi-conducteurs, les batteries lithium-soufre, les nouvelles méthodes de revêtement d'électrodes et les équipements de fabrication avancés.
Les batteries à semi-conducteurs sont développées comme une alternative prometteuse aux batteries lithium-ion traditionnelles en raison de leur densité énergétique plus élevée et de leur sécurité améliorée.
Les batteries au lithium-soufre ont également attiré l’attention en raison de leur potentiel à offrir des densités d’énergie plus élevées et des coûts inférieurs.
De plus, de nouvelles méthodes de revêtement d’électrodes et des équipements de fabrication avancés sont à l’étude pour améliorer l’efficacité et l’évolutivité des processus de production de batteries.
Piles à semi-conducteurs
Les batteries à semi-conducteurs sont devenues une alternative prometteuse aux batteries lithium-ion traditionnelles en raison de leur potentiel d’augmentation de la densité énergétique et de leur sécurité améliorée. Ces batteries utilisent des électrolytes solides au lieu des électrolytes liquides ou en gel que l'on trouve dans les batteries lithium-ion conventionnelles.
Les batteries à semi-conducteurs offrent plusieurs avantages qui en font une option intéressante pour diverses applications :
- Densité énergétique améliorée : les batteries à semi-conducteurs peuvent stocker plus d’énergie par unité de volume que les batteries lithium-ion traditionnelles. Cette densité énergétique accrue permet des sources d’énergie plus durables, ce qui les rend idéales pour les véhicules électriques et les appareils électroniques portables.
- Sécurité améliorée : L'utilisation d'électrolytes solides élimine le risque de fuite ou d'emballement thermique associé aux électrolytes liquides ou en gel dans les batteries lithium-ion. Les batteries à semi-conducteurs sont moins susceptibles de prendre feu ou d’exploser, ce qui améliore la sécurité globale.
- Temps de charge plus rapides : la technologie des batteries à semi-conducteurs permet des temps de charge plus rapides par rapport aux batteries lithium-ion conventionnelles. Cette fonctionnalité est particulièrement avantageuse pour les véhicules électriques, car elle réduit les temps d’arrêt pendant la recharge et améliore le confort général.
- Durée de vie plus longue : La stabilité inhérente des matériaux des batteries à semi-conducteurs contribue à une durée de vie plus longue par rapport aux batteries lithium-ion traditionnelles. Cette longévité fait des batteries à semi-conducteurs une option rentable, car elles nécessitent moins de remplacements au fil du temps.
- Flexibilité de conception : contrairement aux systèmes à base d'électrolyte liquide ou gel, la technologie des batteries à semi-conducteurs offre une flexibilité de conception et de facteur de forme. Les fabricants ont la liberté de créer des formes et des tailles personnalisées, permettant une meilleure intégration dans divers appareils et applications.
Batteries lithium-soufre
Les batteries au lithium-soufre (Li-S) constituent une autre alternative prometteuse aux batteries lithium-ion conventionnelles. Ils fonctionnent sur la base d’une réaction redox réversible entre le lithium et le soufre, où le soufre agit comme matériau cathodique. Les batteries Li-S offrent plusieurs avantages par rapport à leurs homologues, notamment une densité énergétique théorique élevée (environ 2 600 Wh/kg), un faible coût grâce aux ressources abondantes en soufre et le respect de l'environnement.
Pour illustrer davantage les avantages des batteries Li-S par rapport aux batteries lithium-ion traditionnelles, nous pouvons consulter un tableau comparatif :
Caractéristique | Batteries lithium-ion | Batteries lithium-soufre |
---|---|---|
Densité d'énergie | Modéré | Haut |
Coût | Relativement élevé | Faible |
Impact environnemental | Préoccupations concernant les éléments de terres rares utilisés | Des ressources en soufre abondantes |
Sécurité | Risque d'emballement thermique | Sécurité améliorée grâce à une réactivité moindre |
Nouvelles méthodes de revêtement d’électrodes
et l'exploration dans le domaine de la technologie des batteries au lithium, offrant des avancées potentielles dans les systèmes de stockage d'énergie. Ces méthodes consistent à appliquer divers revêtements sur les électrodes de batteries à lithium pour améliorer leurs performances et leur durée de vie.
Certains développements notables dans ce domaine comprennent :
- Revêtement en couche mince : Une technique consiste à déposer un film mince sur la surface de l'électrode pour améliorer sa stabilité et éviter les réactions secondaires avec l'électrolyte. Cela peut aider à atténuer des problèmes tels que la perte de capacité et la formation de dendrites, qui sont des problèmes courants dans les batteries au lithium.
- Des revêtements protecteurs: Une autre approche consiste à appliquer des revêtements protecteurs qui agissent comme des barrières contre l’humidité, l’oxygène et d’autres contaminants. Ces revêtements augmentent non seulement la résistance de la batterie à la dégradation, mais améliorent également sa sécurité en réduisant le risque d'emballement thermique ou de court-circuit.
- Revêtements conducteurs : Pour améliorer la conductivité électrique au sein de la batterie, les chercheurs ont exploré différents types de revêtements conducteurs pour les électrodes. Ces revêtements facilitent un transfert d'électrons efficace entre les matériaux actifs et les collecteurs de courant, améliorant ainsi les performances globales de la batterie.
- Revêtements auto-cicatrisants : Un développement plus récent concerne les revêtements auto-cicatrisants qui peuvent réparer de manière autonome les petites fissures ou les dommages sur la surface de l’électrode. Ces revêtements contiennent des microcapsules remplies d'agents cicatrisants qui sont libérés en cas de dommage, restaurant efficacement l'intégrité structurelle de l'électrode et prolongeant vie de la batterie.
Équipement de fabrication avancé
Un aspect notable du développement des équipements de fabrication avancés est leur potentiel à révolutionner la production et l’assemblage de composants dans les dispositifs de stockage d’énergie. Ces machines et technologies de pointe sont conçues pour améliorer l’efficacité, la précision et la rapidité du processus de fabrication, conduisant finalement à une amélioration des performances des batteries et à une réduction des coûts.
Par exemple, l’un de ces équipements est la machine automatisée d’empilage d’électrodes qui peut empiler avec précision plusieurs couches d’électrodes avec une intervention humaine minimale. Cela élimine non seulement les erreurs humaines, mais augmente également la productivité en réduisant le temps d'assemblage.
De plus, des systèmes robotiques avancés équipés d'algorithmes d'intelligence artificielle peuvent être utilisés pour des contrôles de qualité pendant le processus de fabrication, garantissant ainsi un résultat cohérent et minimisant les défauts.
De plus, l'utilisation de la technologie de soudage laser permet un assemblage précis et fiable des composants de la batterie tout en améliorant les performances globales de la batterie.
Dans l'ensemble, ces progrès dans les équipements de fabrication sont très prometteurs pour atteindre des niveaux plus élevés d'automatisation et de précision dans batterie au lithium production, ouvrant la voie à des solutions de stockage d’énergie plus efficaces qui correspondent à notre désir inconscient de liberté.
Questions fréquemment posées
Combien de temps faut-il pour fabriquer une batterie au lithium du début à la fin ?
Le processus de fabrication d'une batterie au lithium prend généralement plusieurs jours, voire plusieurs semaines, en fonction de divers facteurs tels que le type et la taille de la batterie. Ce processus complexe implique l'assemblage des composants, le remplissage de l'électrolyte, l'étanchéité, les tests et les mesures de contrôle qualité.
Quels sont les 3 principaux composants d’une batterie au lithium ?
Les principaux composants utilisés dans la production de batteries au lithium comprennent une cathode, une anode et un électrolyte. Ces composants travaillent ensemble pour stocker et libérer de l'énergie, ce qui rend batteries à lithium indispensable pour diverses applications.
Existe-t-il des préoccupations environnementales associées au processus de fabrication des batteries au lithium ?
Oui, le processus de fabrication des batteries au lithium suscite des préoccupations environnementales. Il s’agit notamment de l’extraction des ressources, des processus de production à forte intensité énergétique et de l’élimination des piles usagées, qui peuvent libérer des produits chimiques nocifs dans l’environnement si elles ne sont pas correctement gérées.
Comment les fabricants de batteries au lithium garantissent-ils la sécurité et la fiabilité de leurs produits ?
Le principaux fabricants de batteries au lithium en Chine assurer la sécurité et la fiabilité grâce à des mesures de contrôle de qualité rigoureuses. Ils effectuent des tests approfondis, tels que des tests de cyclage thermique et d'abus, pour identifier les problèmes potentiels. De plus, des normes de fabrication strictes sont suivies pour minimiser le risque de défauts et garantir les performances du produit.
Quel est l’inconvénient des batteries au lithium ?
Densité énergétique limitée : par rapport à d’autres compositions chimiques de batteries, les batteries au lithium ont une énergie relativement faible densité, ce qui affecte leur capacité à stocker l’énergie.
Les préoccupations de sécurité: Les batteries au lithium peuvent être sujettes à des emballements thermiques et à des incendies si elles ne sont pas manipulées ou fabriquées correctement.
Impact environnemental: Même si des efforts sont déployés pour réduire l’impact environnemental, l’extraction et l’élimination des matières premières ainsi que les processus de production peuvent avoir des conséquences négatives.
Quelle est la différence entre un batterie au lithium et un lithium-ion batterie?
Les termes « batterie au lithium » et « batterie lithium-ion » sont souvent utilisés de manière interchangeable, mais techniquement, il existe une distinction :
Batterie au lithium: Ce terme fait généralement référence aux piles au lithium jetables, également appelées piles au lithium primaires. Ils ne sont pas rechargeables et sont couramment utilisés dans des appareils tels que les appareils photo et les montres.
Batterie lithium-ion : Ce terme fait référence aux batteries au lithium rechargeables. Ils sont couramment utilisés dans divers appareils, notamment les smartphones, les ordinateurs portables et les véhicules électriques. Les batteries lithium-ion offrent l'avantage d'être rechargeables et ont une durée de vie plus élevée. densité énergétique par rapport au lithium jetable batteries.
En savoir plus Haut Questions sur les piles au lithium!
Conclusion
En conclusion, le lithium processus de fabrication de la batterie est une entreprise complexe et complexe qui nécessite une attention particulière aux détails et le respect de mesures strictes de contrôle de qualité. De la production de cellules individuelles à l'assemblage de packs de batteries, chaque étape du processus joue un rôle crucial pour garantir les performances et la fiabilité du produit final.
Tout au long de cet article, nous avons exploré les différentes étapes impliquées dans batterie au lithium fabrication, y compris la production de cellules et l’assemblage de packs. Nous avons également souligné certains des principaux fabricants sud-africains dans cette industrie et ont discuté des défis auxquels ils sont confrontés ainsi que de leurs solutions innovantes.
Métaphoriquement parlant, le processus de fabrication des batteries au lithium peut être assimilé à la construction d’une maison bien construite. Chaque composant doit être soigneusement conçu et assemblé avec précision pour garantir l’intégrité structurelle et la longévité. Tout comme une fondation solide est essentielle à la stabilité d’une maison, un contrôle qualité rigoureux est également nécessaire pour la performance globale des batteries au lithium.
L'innovation continue de stimuler les progrès de la technologie des batteries, permettant des solutions de stockage d'énergie plus durables et plus efficaces. À mesure que la demande pour ces batteries augmente dans divers secteurs, il devient de plus en plus important pour les fabricants de trouver des moyens de surmonter des défis tels que la réduction des coûts tout en maintenant des normes de qualité élevées.
Dans l’ensemble, comprendre comment les batteries au lithium sont fabriquées fournit des informations précieuses sur leurs capacités et leurs applications potentielles. Grâce aux efforts continus de recherche et de développement axés sur l’amélioration de l’efficacité et de la durabilité, nous pouvons nous attendre à des progrès encore plus importants dans ce domaine à l’avenir.